ಗ್ರೈಂಡಿಂಗ್ ಡಿಸ್ಕ್ಗಳು ವಿವಿಧ ಕೈಗಾರಿಕೆಗಳಲ್ಲಿ ಪ್ರಮುಖ ಪಾತ್ರವಹಿಸುತ್ತವೆ, ವಸ್ತುಗಳ ಆಕಾರ ಮತ್ತು ಪೂರ್ಣಗೊಳಿಸುವಿಕೆಯನ್ನು ಸುಗಮಗೊಳಿಸುತ್ತವೆ. ಆದಾಗ್ಯೂ, ಯಾವುದೇ ಇತರ ಸಾಧನದಂತೆ, ಅವುಗಳ ದಕ್ಷತೆ ಮತ್ತು ಕಾರ್ಯಕ್ಷಮತೆಗೆ ಅಡ್ಡಿಯಾಗುವ ಸಮಸ್ಯೆಗಳಿಂದ ಅವು ಮುಕ್ತವಾಗಿಲ್ಲ. ಈ ಲೇಖನದಲ್ಲಿ, ನಾವು ಸಾಮಾನ್ಯ ಗ್ರೈಂಡಿಂಗ್ ಡಿಸ್ಕ್ ಸಮಸ್ಯೆಗಳನ್ನು ಪರಿಶೀಲಿಸುತ್ತೇವೆ, ಅವುಗಳ ಮೂಲ ಕಾರಣಗಳನ್ನು ಅನ್ವೇಷಿಸುತ್ತೇವೆ ಮತ್ತು ತಡೆರಹಿತ ಕೆಲಸದ ಹರಿವಿಗೆ ಪರಿಣಾಮಕಾರಿ ಪರಿಹಾರಗಳನ್ನು ಒದಗಿಸುತ್ತೇವೆ.
ಪರಿಚಯ
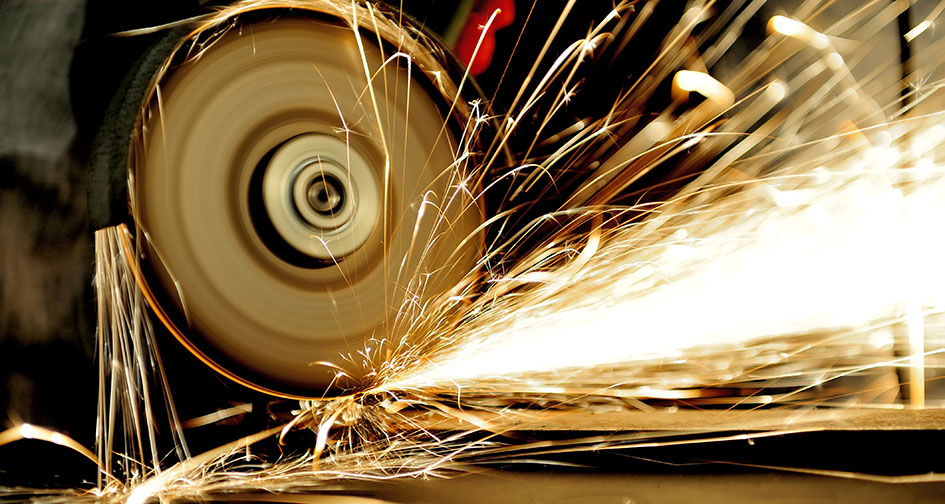
ಗ್ರೈಂಡಿಂಗ್ ಡಿಸ್ಕ್ಗಳು ವಿವಿಧ ಕೈಗಾರಿಕೆಗಳಲ್ಲಿ ಮೂಲಭೂತ ಪಾತ್ರವನ್ನು ವಹಿಸುತ್ತವೆ, ವಸ್ತುಗಳನ್ನು ತೆಗೆಯುವುದು, ರೂಪಿಸುವುದು ಮತ್ತು ಮುಗಿಸುವ ಪ್ರಕ್ರಿಯೆಗಳಿಗೆ ಅಗತ್ಯವಾದ ಸಾಧನಗಳಾಗಿ ಕಾರ್ಯನಿರ್ವಹಿಸುತ್ತವೆ. ಅವುಗಳ ವ್ಯಾಖ್ಯಾನ, ಕೈಗಾರಿಕೆಗಳಲ್ಲಿ ಪ್ರಾಮುಖ್ಯತೆ ಮತ್ತು ಎದುರಿಸುತ್ತಿರುವ ಸಾಮಾನ್ಯ ಸಮಸ್ಯೆಗಳನ್ನು ಅರ್ಥಮಾಡಿಕೊಳ್ಳುವುದು ಅವುಗಳ ಬಳಕೆಯನ್ನು ಅತ್ಯುತ್ತಮವಾಗಿಸಲು ಮತ್ತು ಪರಿಣಾಮಕಾರಿ ಕಾರ್ಯಾಚರಣೆಗಳನ್ನು ಖಚಿತಪಡಿಸಿಕೊಳ್ಳಲು ನಿರ್ಣಾಯಕವಾಗಿದೆ.
A. ಗ್ರೈಂಡಿಂಗ್ ಡಿಸ್ಕ್ಗಳ ವ್ಯಾಖ್ಯಾನ
ಗ್ರೈಂಡಿಂಗ್ ಡಿಸ್ಕ್ಗಳು ವಸ್ತುಗಳ ಮೇಲ್ಮೈಗಳನ್ನು ಕತ್ತರಿಸಲು, ಪುಡಿ ಮಾಡಲು ಅಥವಾ ಹೊಳಪು ಮಾಡಲು ಯಂತ್ರ ಪ್ರಕ್ರಿಯೆಗಳಲ್ಲಿ ಬಳಸುವ ಅಪಘರ್ಷಕ ಸಾಧನಗಳಾಗಿವೆ. ಈ ಡಿಸ್ಕ್ಗಳು ಸಾಮಾನ್ಯವಾಗಿ ಹಿಮ್ಮೇಳ ವಸ್ತುವಿಗೆ ಬಂಧಿತವಾದ ಅಪಘರ್ಷಕ ಕಣಗಳನ್ನು ಒಳಗೊಂಡಿರುತ್ತವೆ, ಹೆಚ್ಚುವರಿ ವಸ್ತುಗಳನ್ನು ತೆಗೆದುಹಾಕುವ, ಮೇಲ್ಮೈಗಳನ್ನು ಸುಗಮಗೊಳಿಸುವ ಅಥವಾ ಅಂಚುಗಳನ್ನು ಹರಿತಗೊಳಿಸುವ ತಿರುಗುವ ಉಪಕರಣವನ್ನು ರಚಿಸುತ್ತವೆ. ಅವು ವಿವಿಧ ಆಕಾರಗಳು ಮತ್ತು ಗಾತ್ರಗಳಲ್ಲಿ ಬರುತ್ತವೆ, ಪ್ರತಿಯೊಂದೂ ನಿರ್ದಿಷ್ಟ ಅನ್ವಯಿಕೆಗಳಿಗಾಗಿ ವಿನ್ಯಾಸಗೊಳಿಸಲಾಗಿದೆ.
ಬಿ. ವಿವಿಧ ಕೈಗಾರಿಕೆಗಳಲ್ಲಿ ಪ್ರಾಮುಖ್ಯತೆ
ಲೋಹ ಕೆಲಸ ಉದ್ಯಮ:
ಲೋಹದ ತಯಾರಿಕೆ ಮತ್ತು ತಯಾರಿಕೆಯಲ್ಲಿ, ಲೋಹದ ಮೇಲ್ಮೈಗಳನ್ನು ರೂಪಿಸಲು, ಡಿಬರ್ರಿಂಗ್ ಮಾಡಲು ಮತ್ತು ಮುಗಿಸಲು ಗ್ರೈಂಡಿಂಗ್ ಡಿಸ್ಕ್ಗಳು ಅತ್ಯಗತ್ಯ. ನಿಖರವಾದ ಆಯಾಮಗಳು ಮತ್ತು ಮೇಲ್ಮೈ ಗುಣಮಟ್ಟವನ್ನು ಸಾಧಿಸಲು ಅವುಗಳನ್ನು ಸಾಮಾನ್ಯವಾಗಿ ಕೋನ ಗ್ರೈಂಡರ್ಗಳೊಂದಿಗೆ ಬಳಸಲಾಗುತ್ತದೆ.
ನಿರ್ಮಾಣ ಉದ್ಯಮ:
ಕಾಂಕ್ರೀಟ್ ಮೇಲ್ಮೈ ತಯಾರಿಕೆ, ಒರಟು ಅಂಚುಗಳನ್ನು ಸುಗಮಗೊಳಿಸುವುದು ಮತ್ತು ಕಲ್ಲು ಮತ್ತು ಕಾಂಕ್ರೀಟ್ನಂತಹ ವಸ್ತುಗಳಲ್ಲಿನ ಅಪೂರ್ಣತೆಗಳನ್ನು ತೆಗೆದುಹಾಕುವಂತಹ ಕಾರ್ಯಗಳಿಗಾಗಿ ನಿರ್ಮಾಣ ವೃತ್ತಿಪರರು ಗ್ರೈಂಡಿಂಗ್ ಡಿಸ್ಕ್ಗಳನ್ನು ಅವಲಂಬಿಸಿರುತ್ತಾರೆ.
ಆಟೋಮೋಟಿವ್ ಉದ್ಯಮ:
ಆಟೋಮೋಟಿವ್ ವಲಯದಲ್ಲಿ ಉಪಕರಣಗಳನ್ನು ಹರಿತಗೊಳಿಸುವುದರಿಂದ ಹಿಡಿದು ಲೋಹದ ಘಟಕಗಳನ್ನು ರೂಪಿಸುವುದು ಮತ್ತು ಮುಗಿಸುವವರೆಗೆ ಗ್ರೈಂಡಿಂಗ್ ಡಿಸ್ಕ್ಗಳು ಅತ್ಯಗತ್ಯ. ಅವು ಆಟೋಮೋಟಿವ್ ಭಾಗಗಳ ನಿಖರತೆ ಮತ್ತು ಗುಣಮಟ್ಟಕ್ಕೆ ಕೊಡುಗೆ ನೀಡುತ್ತವೆ.
ಮರಗೆಲಸ ಉದ್ಯಮ:
ಮರದ ಕೆಲಸಗಾರರು ಮರದ ಮೇಲ್ಮೈಗಳನ್ನು ರೂಪಿಸಲು ಮತ್ತು ಸುಗಮಗೊಳಿಸಲು ಗ್ರೈಂಡಿಂಗ್ ಡಿಸ್ಕ್ಗಳನ್ನು ಬಳಸುತ್ತಾರೆ. ಈ ಡಿಸ್ಕ್ಗಳು ಹೆಚ್ಚುವರಿ ವಸ್ತುಗಳನ್ನು ತೆಗೆದುಹಾಕುವಲ್ಲಿ, ಆಕಾರಗಳನ್ನು ಪರಿಷ್ಕರಿಸುವಲ್ಲಿ ಮತ್ತು ಮುಂದಿನ ಪೂರ್ಣಗೊಳಿಸುವಿಕೆಗಾಗಿ ಮರವನ್ನು ಸಿದ್ಧಪಡಿಸುವಲ್ಲಿ ಪರಿಣಾಮಕಾರಿ.
ಸಾಮಾನ್ಯ ಉತ್ಪಾದನೆ:
ಗ್ರೈಂಡಿಂಗ್ ಡಿಸ್ಕ್ಗಳು ವಿವಿಧ ಉತ್ಪಾದನಾ ಪ್ರಕ್ರಿಯೆಗಳಲ್ಲಿ ಅನ್ವಯಿಕೆಗಳನ್ನು ಕಂಡುಕೊಳ್ಳುತ್ತವೆ, ಅಲ್ಲಿ ನಿಖರವಾದ ವಸ್ತು ತೆಗೆಯುವಿಕೆ ಅಗತ್ಯವಿರುತ್ತದೆ, ಇದು ಉತ್ತಮ-ಗುಣಮಟ್ಟದ ಘಟಕಗಳ ಉತ್ಪಾದನೆಗೆ ಕೊಡುಗೆ ನೀಡುತ್ತದೆ.
ಸಿ. ಎದುರಿಸುವ ಸಾಮಾನ್ಯ ಸಮಸ್ಯೆಗಳು
ಡಿಸ್ಕ್ ಸವೆತ ಮತ್ತು ಸವೆತ:
ನಿರಂತರ ಬಳಕೆಯು ಗ್ರೈಂಡಿಂಗ್ ಡಿಸ್ಕ್ನ ಸವೆತ ಮತ್ತು ಸವೆತಕ್ಕೆ ಕಾರಣವಾಗಬಹುದು, ಇದು ಅದರ ಕಾರ್ಯಕ್ಷಮತೆಯ ಮೇಲೆ ಪರಿಣಾಮ ಬೀರುತ್ತದೆ. ದಕ್ಷತೆಯನ್ನು ಕಾಪಾಡಿಕೊಳ್ಳಲು ನಿಯಮಿತ ತಪಾಸಣೆ ಮತ್ತು ಬದಲಿ ಅಗತ್ಯ.
ಅಧಿಕ ಬಿಸಿಯಾಗುವುದು:
ದೀರ್ಘಕಾಲದ ಬಳಕೆಯ ಸಮಯದಲ್ಲಿ ಅತಿಯಾದ ಘರ್ಷಣೆಯು ಡಿಸ್ಕ್ ಅನ್ನು ಅತಿಯಾಗಿ ಬಿಸಿಯಾಗಿಸಲು ಕಾರಣವಾಗಬಹುದು, ಇದು ಡಿಸ್ಕ್ನ ಬಾಳಿಕೆ ಮತ್ತು ಸಿದ್ಧಪಡಿಸಿದ ಮೇಲ್ಮೈಯ ಗುಣಮಟ್ಟದ ಮೇಲೆ ಪರಿಣಾಮ ಬೀರುತ್ತದೆ. ಸರಿಯಾದ ತಂಪಾಗಿಸುವ ಕ್ರಮಗಳು ಮತ್ತು ಆವರ್ತಕ ವಿರಾಮಗಳು ಅತ್ಯಗತ್ಯ.
ಅಡಚಣೆ:
ಗ್ರೈಂಡಿಂಗ್ ಡಿಸ್ಕ್ಗಳು ವಸ್ತುಗಳ ಅವಶೇಷಗಳನ್ನು ಸಂಗ್ರಹಿಸಬಹುದು, ಅವುಗಳ ಪರಿಣಾಮಕಾರಿತ್ವವನ್ನು ಕಡಿಮೆ ಮಾಡಬಹುದು. ನಿಯಮಿತವಾಗಿ ಸ್ವಚ್ಛಗೊಳಿಸುವುದು ಅಥವಾ ಅಡಚಣೆ-ನಿರೋಧಕ ವೈಶಿಷ್ಟ್ಯಗಳನ್ನು ಹೊಂದಿರುವ ಡಿಸ್ಕ್ಗಳನ್ನು ಆಯ್ಕೆ ಮಾಡುವುದು ಈ ಸಮಸ್ಯೆಯನ್ನು ತಡೆಯಲು ಸಹಾಯ ಮಾಡುತ್ತದೆ.
ಕಂಪನ ಮತ್ತು ಕಂಪನ:
ಅಸಮತೋಲನ ಅಥವಾ ಅಸಮಾನವಾದ ಸವೆತವು ಕಂಪನ ಅಥವಾ ನಡುಕಕ್ಕೆ ಕಾರಣವಾಗಬಹುದು, ಇದು ಮುಕ್ತಾಯದ ಗುಣಮಟ್ಟ ಮತ್ತು ಕಾರ್ಯಾಚರಣೆಯ ಸುರಕ್ಷತೆ ಎರಡರ ಮೇಲೂ ಪರಿಣಾಮ ಬೀರುತ್ತದೆ. ಸರಿಯಾದ ಸ್ಥಾಪನೆ ಮತ್ತು ಸಮತೋಲನವು ನಿರ್ಣಾಯಕವಾಗಿದೆ.
ತಪ್ಪಾದ ಡಿಸ್ಕ್ ಆಯ್ಕೆ:
ನಿರ್ದಿಷ್ಟ ವಸ್ತು ಅಥವಾ ಅನ್ವಯಕ್ಕೆ ತಪ್ಪು ರೀತಿಯ ಗ್ರೈಂಡಿಂಗ್ ಡಿಸ್ಕ್ ಅನ್ನು ಆಯ್ಕೆ ಮಾಡುವುದರಿಂದ ಅಸಮರ್ಥತೆ ಮತ್ತು ಸಂಭಾವ್ಯ ಹಾನಿಗೆ ಕಾರಣವಾಗಬಹುದು. ವಸ್ತು ಹೊಂದಾಣಿಕೆಯ ಆಧಾರದ ಮೇಲೆ ಸರಿಯಾದ ಆಯ್ಕೆ ಅತ್ಯಗತ್ಯ.
ಗ್ರೈಂಡಿಂಗ್ ಡಿಸ್ಕ್ಗಳ ವ್ಯಾಖ್ಯಾನ, ಮಹತ್ವ ಮತ್ತು ಸಂಭಾವ್ಯ ಸವಾಲುಗಳನ್ನು ಅರ್ಥಮಾಡಿಕೊಳ್ಳುವುದು ಈ ಉಪಕರಣಗಳನ್ನು ಅವಲಂಬಿಸಿರುವ ಕೈಗಾರಿಕೆಗಳಿಗೆ ಅತ್ಯಗತ್ಯ. ಸಾಮಾನ್ಯ ಸಮಸ್ಯೆಗಳನ್ನು ಪರಿಹರಿಸುವ ಮೂಲಕ ಮತ್ತು ಸರಿಯಾದ ಬಳಕೆಯನ್ನು ಖಚಿತಪಡಿಸಿಕೊಳ್ಳುವ ಮೂಲಕ, ಕೈಗಾರಿಕೆಗಳು ತಮ್ಮ ಅನ್ವಯಿಕೆಗಳಲ್ಲಿ ಗ್ರೈಂಡಿಂಗ್ ಡಿಸ್ಕ್ಗಳ ಪರಿಣಾಮಕಾರಿತ್ವವನ್ನು ಹೆಚ್ಚಿಸಬಹುದು.
ಗ್ರೈಂಡಿಂಗ್ ಡಿಸ್ಕ್ಗಳ ಮೇಲೆ ಸವೆತ ಮತ್ತು ಹರಿದುಹೋಗುವಿಕೆ
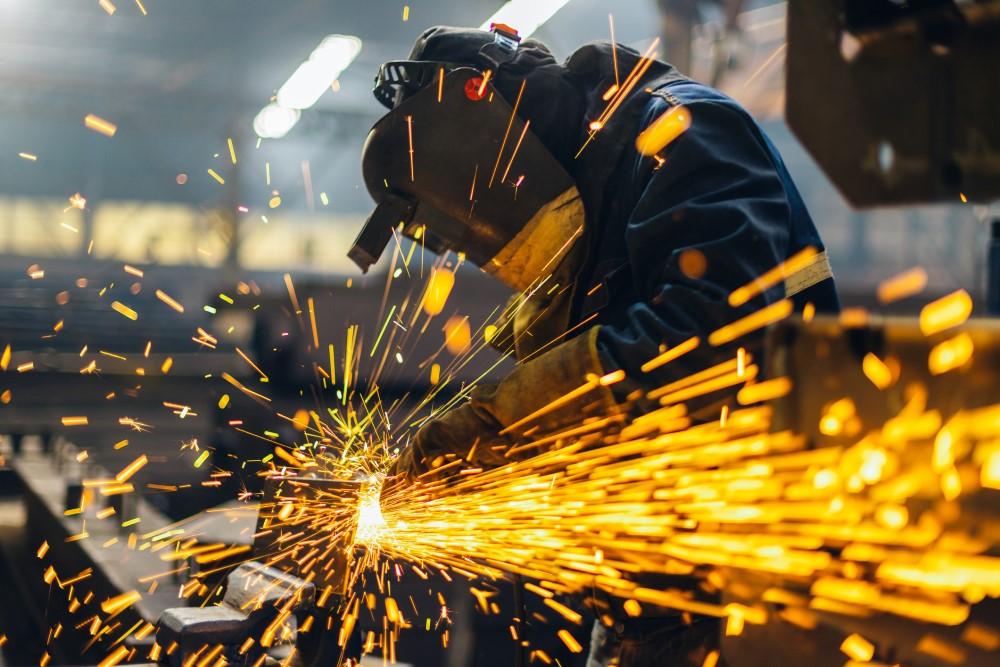
ಗ್ರೈಂಡಿಂಗ್ ಡಿಸ್ಕ್ಗಳು ವಿವಿಧ ಕೈಗಾರಿಕೆಗಳಲ್ಲಿ ಅತ್ಯಗತ್ಯ ಸಾಧನಗಳಾಗಿದ್ದು, ಲೋಹದ ತಯಾರಿಕೆಯಿಂದ ಹಿಡಿದು ಕಾಂಕ್ರೀಟ್ ಪಾಲಿಶಿಂಗ್ವರೆಗಿನ ಕಾರ್ಯಗಳಿಗೆ ಅಗತ್ಯವಾದ ಸವೆತವನ್ನು ಒದಗಿಸುತ್ತವೆ. ಗ್ರೈಂಡಿಂಗ್ ಡಿಸ್ಕ್ಗಳ ಸವೆತ ಮತ್ತು ಹರಿದುಹೋಗುವಿಕೆಗೆ ಕಾರಣವಾಗುವ ಅಂಶಗಳನ್ನು ಅರ್ಥಮಾಡಿಕೊಳ್ಳುವುದು ಅವುಗಳ ಕಾರ್ಯಕ್ಷಮತೆಯನ್ನು ಅತ್ಯುತ್ತಮವಾಗಿಸಲು ಮತ್ತು ಸುರಕ್ಷತೆಯನ್ನು ಖಚಿತಪಡಿಸಿಕೊಳ್ಳಲು ನಿರ್ಣಾಯಕವಾಗಿದೆ.
ವಸ್ತುವಿನ ಗಡಸುತನ ಮತ್ತು ಸಂಯೋಜನೆ:
ಗಡಸುತನದ ವ್ಯತ್ಯಾಸ:ಗ್ರೈಂಡಿಂಗ್ ಡಿಸ್ಕ್ಗಳು ವಿಭಿನ್ನ ಗಡಸುತನದ ಮಟ್ಟಗಳನ್ನು ಹೊಂದಿರುವ ವಸ್ತುಗಳನ್ನು ಎದುರಿಸುತ್ತವೆ. ಲೋಹ ಮತ್ತು ಕಾಂಕ್ರೀಟ್ನಂತಹ ಸವೆತ ವಸ್ತುಗಳು ಗಡಸುತನದಲ್ಲಿ ಗಮನಾರ್ಹವಾಗಿ ಭಿನ್ನವಾಗಿರುತ್ತವೆ. ಗಟ್ಟಿಯಾದ ವಸ್ತುಗಳ ವಿರುದ್ಧ ನಿರಂತರವಾಗಿ ರುಬ್ಬುವುದರಿಂದ ಸವೆತ ವೇಗಗೊಳ್ಳುತ್ತದೆ.
ವಸ್ತು ಸಂಯೋಜನೆ:ರುಬ್ಬುವ ವಸ್ತುವಿನಲ್ಲಿ ಅಪಘರ್ಷಕ ಅಂಶಗಳ ಉಪಸ್ಥಿತಿಯು ಗ್ರೈಂಡಿಂಗ್ ಡಿಸ್ಕ್ ಮೇಲಿನ ಸವೆತದ ಮೇಲೆ ಪರಿಣಾಮ ಬೀರುತ್ತದೆ. ಅಪಘರ್ಷಕ ಕಣಗಳು ಡಿಸ್ಕ್ ಸವೆಯುವುದನ್ನು ವೇಗಗೊಳಿಸಬಹುದು.
ರುಬ್ಬುವ ಒತ್ತಡ ಮತ್ತು ಬಲ:
ಅತಿಯಾದ ಒತ್ತಡ:ಗ್ರೈಂಡಿಂಗ್ ಡಿಸ್ಕ್ ಮೇಲೆ ಅತಿಯಾದ ಒತ್ತಡ ಹೇರುವುದರಿಂದ ವೇಗವಾಗಿ ಸವೆಯುವಿಕೆಗೆ ಕಾರಣವಾಗಬಹುದು. ಡಿಸ್ಕ್ ಮೇಲೆ ಅನಗತ್ಯ ಒತ್ತಡ ಬೀಳದಂತೆ ನಿರ್ದಿಷ್ಟ ಅಪ್ಲಿಕೇಶನ್ಗೆ ಶಿಫಾರಸು ಮಾಡಲಾದ ಒತ್ತಡವನ್ನು ಬಳಸುವುದು ಅತ್ಯಗತ್ಯ.
ಅಸಮರ್ಪಕ ಬಲ: ಮತ್ತೊಂದೆಡೆ, ಸಾಕಷ್ಟು ಬಲವಿಲ್ಲದಿರುವುದು ದೀರ್ಘಕಾಲದವರೆಗೆ ರುಬ್ಬುವಿಕೆಗೆ ಕಾರಣವಾಗಬಹುದು, ಹೆಚ್ಚುವರಿ ಘರ್ಷಣೆ ಮತ್ತು ಶಾಖವನ್ನು ಉತ್ಪಾದಿಸುತ್ತದೆ, ಇದು ಸವೆತಕ್ಕೆ ಕಾರಣವಾಗುತ್ತದೆ.
ಡಿಸ್ಕ್ ಗುಣಮಟ್ಟ ಮತ್ತು ಸಂಯೋಜನೆ:
ಸವೆತದ ವಸ್ತುಗಳ ಗುಣಮಟ್ಟ:ಗ್ರೈಂಡಿಂಗ್ ಡಿಸ್ಕ್ನಲ್ಲಿ ಬಳಸುವ ಅಪಘರ್ಷಕ ವಸ್ತುಗಳ ಗುಣಮಟ್ಟವು ಅದರ ಜೀವಿತಾವಧಿಯನ್ನು ಗಮನಾರ್ಹವಾಗಿ ಪ್ರಭಾವಿಸುತ್ತದೆ. ಉತ್ತಮ ಗುಣಮಟ್ಟದ ಅಪಘರ್ಷಕ ವಸ್ತುಗಳು ಸವೆತವನ್ನು ವಿರೋಧಿಸುತ್ತವೆ ಮತ್ತು ಹೆಚ್ಚು ಕಾಲ ತೀಕ್ಷ್ಣತೆಯನ್ನು ಕಾಯ್ದುಕೊಳ್ಳುತ್ತವೆ.
ಬಾಂಡಿಂಗ್ ಏಜೆಂಟ್:ಅಪಘರ್ಷಕ ಕಣಗಳನ್ನು ಒಟ್ಟಿಗೆ ಹಿಡಿದಿಟ್ಟುಕೊಳ್ಳುವ ಬಂಧಕ ಏಜೆಂಟ್ ನಿರ್ಣಾಯಕ ಪಾತ್ರವನ್ನು ವಹಿಸುತ್ತದೆ. ಉತ್ತಮವಾಗಿ ವಿನ್ಯಾಸಗೊಳಿಸಲಾದ ಬಂಧಕ ಏಜೆಂಟ್ ಡಿಸ್ಕ್ನ ಬಾಳಿಕೆಯನ್ನು ಹೆಚ್ಚಿಸುತ್ತದೆ.
ಕೆಲಸದ ಪರಿಸರದ ಪರಿಸ್ಥಿತಿಗಳು:
ತಾಪಮಾನ:ರುಬ್ಬುವ ಸಮಯದಲ್ಲಿ ಉತ್ಪತ್ತಿಯಾಗುವ ಎತ್ತರದ ತಾಪಮಾನವು ಡಿಸ್ಕ್ನ ಸಂಯೋಜನೆಯ ಮೇಲೆ ಪರಿಣಾಮ ಬೀರುತ್ತದೆ. ಅತಿಯಾದ ಶಾಖವು ಬಂಧಕ ಏಜೆಂಟ್ ಅನ್ನು ದುರ್ಬಲಗೊಳಿಸುತ್ತದೆ ಮತ್ತು ಸವೆತವನ್ನು ವೇಗಗೊಳಿಸುತ್ತದೆ.
ತೇವಾಂಶ ಮತ್ತು ಮಾಲಿನ್ಯಕಾರಕಗಳು:ಕೆಲಸದ ವಾತಾವರಣದಲ್ಲಿ ತೇವಾಂಶ ಅಥವಾ ಮಾಲಿನ್ಯಕಾರಕಗಳಿಗೆ ಒಡ್ಡಿಕೊಳ್ಳುವುದರಿಂದ ಗ್ರೈಂಡಿಂಗ್ ಡಿಸ್ಕ್ನ ಸಮಗ್ರತೆಯ ಮೇಲೆ ಪರಿಣಾಮ ಬೀರಬಹುದು, ಇದು ವೇಗವಾಗಿ ಸವೆಯಲು ಕಾರಣವಾಗುತ್ತದೆ.
ಆಪರೇಟರ್ ತಂತ್ರ:
ಸರಿಯಾದ ತಂತ್ರ:ಆಪರೇಟರ್ ಕೌಶಲ್ಯ ಮತ್ತು ತಂತ್ರವು ಅತ್ಯಗತ್ಯ. ತಪ್ಪಾದ ಕೋನಗಳಲ್ಲಿ ರುಬ್ಬುವುದು ಅಥವಾ ಅತಿಯಾದ ಬಲವನ್ನು ಬಳಸುವುದು ಮುಂತಾದ ಅನುಚಿತ ಬಳಕೆಯು ಅಸಮವಾದ ಸವೆತಕ್ಕೆ ಕಾರಣವಾಗಬಹುದು ಮತ್ತು ಡಿಸ್ಕ್ ಬಾಳಿಕೆಯನ್ನು ಕಡಿಮೆ ಮಾಡಬಹುದು.
ನಿಯಮಿತ ತಪಾಸಣೆಗಳು:ನಿರ್ವಾಹಕರು ಗ್ರೈಂಡಿಂಗ್ ಡಿಸ್ಕ್ ಅನ್ನು ಯಾವುದೇ ಹಾನಿ ಅಥವಾ ಸವೆತದ ಚಿಹ್ನೆಗಳಿಗಾಗಿ ನಿಯಮಿತವಾಗಿ ಪರಿಶೀಲಿಸಬೇಕು. ಒಂದು ನಿರ್ದಿಷ್ಟ ಹಂತವನ್ನು ಮೀರಿ ಸವೆತವನ್ನು ತೋರಿಸುವ ಡಿಸ್ಕ್ಗಳನ್ನು ತಕ್ಷಣವೇ ಬದಲಾಯಿಸಬೇಕು.
ಡಿಸ್ಕ್ ಗಾತ್ರ ಮತ್ತು RPM ಹೊಂದಾಣಿಕೆ:
ಸರಿಯಾದ ಗಾತ್ರ:ಗ್ರೈಂಡರ್ಗೆ ಸರಿಯಾದ ಡಿಸ್ಕ್ ಗಾತ್ರವನ್ನು ಬಳಸುವುದು ಬಹಳ ಮುಖ್ಯ. ತಪ್ಪಾದ ಗಾತ್ರದ ಡಿಸ್ಕ್ಗಳು ಅಸಮಾನವಾಗಿ ಸವೆಯಬಹುದು ಅಥವಾ ಸುರಕ್ಷತಾ ಅಪಾಯಗಳನ್ನು ಉಂಟುಮಾಡಬಹುದು.
RPM ಹೊಂದಾಣಿಕೆ:ಗ್ರೈಂಡಿಂಗ್ ಡಿಸ್ಕ್ಗಾಗಿ ಶಿಫಾರಸು ಮಾಡಲಾದ ಪ್ರತಿ ನಿಮಿಷಕ್ಕೆ (RPM) ಕ್ರಾಂತಿಗಳನ್ನು ಅನುಸರಿಸುವುದು ಅತ್ಯುತ್ತಮ ಕಾರ್ಯಕ್ಷಮತೆಯನ್ನು ಖಚಿತಪಡಿಸುತ್ತದೆ ಮತ್ತು ಅಕಾಲಿಕ ಸವೆತವನ್ನು ತಡೆಯುತ್ತದೆ.
ನಿಯಮಿತ ನಿರ್ವಹಣೆ, ಶಿಫಾರಸು ಮಾಡಲಾದ ಕಾರ್ಯಾಚರಣಾ ಪರಿಸ್ಥಿತಿಗಳ ಅನುಸರಣೆ ಮತ್ತು ಕಾರ್ಯಕ್ಕಾಗಿ ಸರಿಯಾದ ಗ್ರೈಂಡಿಂಗ್ ಡಿಸ್ಕ್ ಅನ್ನು ಆಯ್ಕೆ ಮಾಡುವುದು ಸವೆತ ಮತ್ತು ಕಣ್ಣೀರನ್ನು ಕಡಿಮೆ ಮಾಡಲು ಅಗತ್ಯವಾದ ಅಭ್ಯಾಸಗಳಾಗಿವೆ. ಸವೆತದ ಮೇಲೆ ಪ್ರಭಾವ ಬೀರುವ ಅಂಶಗಳನ್ನು ಅರ್ಥಮಾಡಿಕೊಳ್ಳುವ ಮೂಲಕ, ನಿರ್ವಾಹಕರು ಗ್ರೈಂಡಿಂಗ್ ಡಿಸ್ಕ್ಗಳ ದೀರ್ಘಾಯುಷ್ಯ ಮತ್ತು ದಕ್ಷತೆಯನ್ನು ಹೆಚ್ಚಿಸಬಹುದು, ಸುರಕ್ಷಿತ ಮತ್ತು ಹೆಚ್ಚು ಉತ್ಪಾದಕ ಗ್ರೈಂಡಿಂಗ್ ಕಾರ್ಯಾಚರಣೆಗಳಿಗೆ ಕೊಡುಗೆ ನೀಡಬಹುದು.
ಅಸಮ ರುಬ್ಬುವಿಕೆ
ಅಸಮಾನ ರುಬ್ಬುವಿಕೆಯು ನೆಲಕ್ಕೆ ಹಾಕಲಾದ ಮೇಲ್ಮೈ ಸ್ಥಿರ ಮತ್ತು ನಯವಾದ ಮುಕ್ತಾಯವನ್ನು ಸಾಧಿಸದ ಪರಿಸ್ಥಿತಿಯನ್ನು ಸೂಚಿಸುತ್ತದೆ. ಈ ಸಮಸ್ಯೆಯು ವಿವಿಧ ಕಾರಣಗಳಿಗಾಗಿ ಉದ್ಭವಿಸಬಹುದು ಮತ್ತು ವರ್ಕ್ಪೀಸ್ನ ಗುಣಮಟ್ಟದ ಮೇಲೆ ಪರಿಣಾಮ ಬೀರಬಹುದು. ಅಸಮಾನ ರುಬ್ಬುವಿಕೆಗೆ ಕಾರಣವಾಗುವ ಸಾಮಾನ್ಯ ಅಂಶಗಳು ಮತ್ತು ಸಂಭಾವ್ಯ ಪರಿಹಾರಗಳು ಇಲ್ಲಿವೆ:
ತಪ್ಪಾದ ಗ್ರೈಂಡಿಂಗ್ ವೀಲ್ ಆಯ್ಕೆ:
ಪರಿಹಾರ:ರುಬ್ಬುವ ಚಕ್ರವು ರುಬ್ಬುವ ವಸ್ತುವಿಗೆ ಸೂಕ್ತವಾಗಿದೆ ಎಂದು ಖಚಿತಪಡಿಸಿಕೊಳ್ಳಿ. ವಿಭಿನ್ನ ವಸ್ತುಗಳಿಗೆ ನಿರ್ದಿಷ್ಟ ಅಪಘರ್ಷಕ ಗುಣಲಕ್ಷಣಗಳು ಬೇಕಾಗುತ್ತವೆ. ಅನ್ವಯಕ್ಕೆ ಸರಿಯಾದ ಚಕ್ರದ ಪ್ರಕಾರ, ಗ್ರಿಟ್ ಗಾತ್ರ ಮತ್ತು ಬಂಧವನ್ನು ಆರಿಸಿ.
ಅನುಚಿತ ಚಕ್ರ ಡ್ರೆಸ್ಸಿಂಗ್:
ಕಾರಣ:ಸರಿಯಾಗಿ ಧರಿಸದ ಗ್ರೈಂಡಿಂಗ್ ವೀಲ್ ಅಸಮವಾದ ಸವೆತ ಮತ್ತು ನಿಷ್ಪರಿಣಾಮಕಾರಿ ಕತ್ತರಿಸುವಿಕೆಗೆ ಕಾರಣವಾಗಬಹುದು.
ಪರಿಹಾರ:ಗ್ರೈಂಡಿಂಗ್ ವೀಲ್ನ ಆಕಾರವನ್ನು ಕಾಪಾಡಿಕೊಳ್ಳಲು ಮತ್ತು ಸಂಗ್ರಹವಾದ ಯಾವುದೇ ಕಸವನ್ನು ತೆಗೆದುಹಾಕಲು ನಿಯಮಿತವಾಗಿ ಅದನ್ನು ಡ್ರೆಸ್ಸಿಂಗ್ ಮಾಡಿ. ಸರಿಯಾದ ಡ್ರೆಸ್ಸಿಂಗ್ ಸ್ಥಿರವಾದ ಕತ್ತರಿಸುವ ಮೇಲ್ಮೈಯನ್ನು ಖಚಿತಪಡಿಸುತ್ತದೆ.
ರುಬ್ಬುವ ದ್ರವ ಅಥವಾ ಶೀತಕ ಅಸಮರ್ಪಕ:
ಕಾರಣ:ರುಬ್ಬುವ ದ್ರವದ ಸಾಕಷ್ಟಿಲ್ಲದ ಅಥವಾ ಅನುಚಿತ ಬಳಕೆಯು ಘರ್ಷಣೆ ಮತ್ತು ಶಾಖವನ್ನು ಹೆಚ್ಚಿಸಲು ಕಾರಣವಾಗಬಹುದು, ಇದು ಅಸಮವಾದ ರುಬ್ಬುವಿಕೆಗೆ ಕಾರಣವಾಗುತ್ತದೆ.
ಪರಿಹಾರ:ಶಾಖವನ್ನು ಹೊರಹಾಕಲು ಮತ್ತು ಘರ್ಷಣೆಯನ್ನು ಕಡಿಮೆ ಮಾಡಲು ಸೂಕ್ತವಾದ ರುಬ್ಬುವ ದ್ರವ ಅಥವಾ ಶೀತಕವನ್ನು ಬಳಸಿ. ಏಕರೂಪದ ಫಲಿತಾಂಶಗಳನ್ನು ಸಾಧಿಸಲು ಸರಿಯಾದ ತಂಪಾಗಿಸುವಿಕೆ ಅತ್ಯಗತ್ಯ.
ತಪ್ಪಾದ ಗ್ರೈಂಡಿಂಗ್ ನಿಯತಾಂಕಗಳು:
ಕಾರಣ:ಅತಿಯಾದ ವೇಗ, ಫೀಡ್ ದರ ಅಥವಾ ಕತ್ತರಿಸಿದ ಆಳದಂತಹ ತಪ್ಪಾದ ಗ್ರೈಂಡಿಂಗ್ ನಿಯತಾಂಕಗಳನ್ನು ಬಳಸುವುದು ಅಸಮವಾದ ಗ್ರೈಂಡಿಂಗ್ಗೆ ಕಾರಣವಾಗಬಹುದು.
ಪರಿಹಾರ:ವಸ್ತು ಮತ್ತು ಅಪ್ಲಿಕೇಶನ್ ಅವಶ್ಯಕತೆಗಳಿಗೆ ಅನುಗುಣವಾಗಿ ಗ್ರೈಂಡಿಂಗ್ ನಿಯತಾಂಕಗಳನ್ನು ಹೊಂದಿಸಿ. ಸೂಕ್ತ ಸೆಟ್ಟಿಂಗ್ಗಳಿಗಾಗಿ ತಯಾರಕರ ಶಿಫಾರಸುಗಳನ್ನು ನೋಡಿ.
ಸವೆದ ಗ್ರೈಂಡಿಂಗ್ ವೀಲ್:
ಕಾರಣ:ಹಳೆಯದಾದ ಗ್ರೈಂಡಿಂಗ್ ವೀಲ್ ಸ್ಥಿರವಾದ ಕತ್ತರಿಸುವ ಮೇಲ್ಮೈಯನ್ನು ಒದಗಿಸದಿರಬಹುದು, ಇದರ ಪರಿಣಾಮವಾಗಿ ಅಸಮಾನವಾದ ಗ್ರೈಂಡಿಂಗ್ ಉಂಟಾಗುತ್ತದೆ.
ಪರಿಹಾರ:ಗ್ರೈಂಡಿಂಗ್ ವೀಲ್ ಅದರ ಬಳಸಬಹುದಾದ ಜೀವಿತಾವಧಿಯ ಅಂತ್ಯವನ್ನು ತಲುಪಿದಾಗ ಅದನ್ನು ಬದಲಾಯಿಸಿ. ಸವೆತದ ಚಿಹ್ನೆಗಳಿಗಾಗಿ ನಿಯಮಿತವಾಗಿ ಚಕ್ರವನ್ನು ಪರೀಕ್ಷಿಸಿ.
ಅಸಮ ಒತ್ತಡ ಅಥವಾ ಫೀಡ್ ದರ:
ಕಾರಣ:ರುಬ್ಬುವ ಸಮಯದಲ್ಲಿ ಅಸಮ ಒತ್ತಡ ಅಥವಾ ಅಸಮಂಜಸ ಫೀಡ್ ದರಗಳು ಅನಿಯಮಿತ ವಸ್ತು ತೆಗೆಯುವಿಕೆಗೆ ಕಾರಣವಾಗಬಹುದು.
ಪರಿಹಾರ:ಏಕರೂಪದ ಒತ್ತಡವನ್ನು ಅನ್ವಯಿಸಿ ಮತ್ತು ವರ್ಕ್ಪೀಸ್ನಾದ್ಯಂತ ಸ್ಥಿರವಾದ ಫೀಡ್ ದರವನ್ನು ಕಾಪಾಡಿಕೊಳ್ಳಿ. ಆಪರೇಟರ್ ಕೌಶಲ್ಯ ಮತ್ತು ವಿವರಗಳಿಗೆ ಗಮನವು ನಿರ್ಣಾಯಕವಾಗಿದೆ.
ಯಂತ್ರ ಸಮಸ್ಯೆಗಳು:
ಕಾರಣ:ಗ್ರೈಂಡಿಂಗ್ ಯಂತ್ರದ ಯಾಂತ್ರಿಕ ಸಮಸ್ಯೆಗಳು, ಉದಾಹರಣೆಗೆ ತಪ್ಪು ಜೋಡಣೆ ಅಥವಾ ಸ್ಪಿಂಡಲ್ನ ಸಮಸ್ಯೆಗಳು, ಅಸಮಾನ ಗ್ರೈಂಡಿಂಗ್ಗೆ ಕಾರಣವಾಗಬಹುದು.
ಪರಿಹಾರ:ಗ್ರೈಂಡಿಂಗ್ ಯಂತ್ರದ ನಿಯಮಿತ ನಿರ್ವಹಣಾ ಪರಿಶೀಲನೆಗಳನ್ನು ನಡೆಸುವುದು. ಸರಿಯಾದ ಕಾರ್ಯನಿರ್ವಹಣೆಯನ್ನು ಖಚಿತಪಡಿಸಿಕೊಳ್ಳಲು ಯಾವುದೇ ಯಾಂತ್ರಿಕ ಸಮಸ್ಯೆಗಳನ್ನು ತಕ್ಷಣವೇ ಪರಿಹರಿಸಿ.
ವರ್ಕ್ಪೀಸ್ ಫಿಕ್ಚರಿಂಗ್:
ಕಾರಣ:ಸರಿಯಾಗಿ ಸುರಕ್ಷಿತವಲ್ಲದ ಅಥವಾ ತಪ್ಪಾಗಿ ಜೋಡಿಸಲಾದ ವರ್ಕ್ಪೀಸ್ಗಳು ಅಸಮಾನವಾದ ರುಬ್ಬುವಿಕೆಗೆ ಕಾರಣವಾಗಬಹುದು.
ಪರಿಹಾರ:ಕೆಲಸದ ಭಾಗವು ಸರಿಯಾಗಿ ಜೋಡಿಸಲ್ಪಟ್ಟಿರುವುದನ್ನು ಮತ್ತು ಜೋಡಣೆಗೊಂಡಿರುವುದನ್ನು ಖಚಿತಪಡಿಸಿಕೊಳ್ಳಿ. ರುಬ್ಬುವ ಪ್ರಕ್ರಿಯೆಯ ಸಮಯದಲ್ಲಿ ಚಲನೆಯನ್ನು ತಡೆಯಲು ಅದನ್ನು ಬಿಗಿಯಾಗಿ ಭದ್ರಪಡಿಸಿ.
ಅಸಮವಾದ ಗ್ರೈಂಡಿಂಗ್ ಅನ್ನು ಪರಿಹರಿಸಲು ಸರಿಯಾದ ಸಲಕರಣೆಗಳ ಸೆಟಪ್, ಸರಿಯಾದ ಕಾರ್ಯಾಚರಣಾ ನಿಯತಾಂಕಗಳು ಮತ್ತು ನಿಯಮಿತ ನಿರ್ವಹಣಾ ಅಭ್ಯಾಸಗಳ ಸಂಯೋಜನೆಯ ಅಗತ್ಯವಿದೆ. ಗ್ರೈಂಡಿಂಗ್ ಅನ್ವಯಿಕೆಗಳಲ್ಲಿ ಉತ್ತಮ-ಗುಣಮಟ್ಟದ ಮತ್ತು ಸ್ಥಿರವಾದ ಫಲಿತಾಂಶಗಳನ್ನು ಸಾಧಿಸಲು ಸಮಸ್ಯೆಗಳನ್ನು ಗುರುತಿಸಲು ಮತ್ತು ಸರಿಪಡಿಸಲು ನಿರ್ವಾಹಕರಿಗೆ ತರಬೇತಿ ನೀಡಬೇಕು. ನಿಯಮಿತ ತಪಾಸಣೆ ಮತ್ತು ಉತ್ತಮ ಅಭ್ಯಾಸಗಳ ಅನುಸರಣೆ ಗ್ರೈಂಡಿಂಗ್ ಪ್ರಕ್ರಿಯೆಯ ಸಮಯದಲ್ಲಿ ಪರಿಣಾಮಕಾರಿ ಮತ್ತು ಏಕರೂಪದ ವಸ್ತು ತೆಗೆಯುವಿಕೆಗೆ ಕೊಡುಗೆ ನೀಡುತ್ತದೆ.
ಅಧಿಕ ಬಿಸಿಯಾಗುವಿಕೆಯ ಸಮಸ್ಯೆಗಳು
ರುಬ್ಬುವ ಸಮಯದಲ್ಲಿ ಅತಿಯಾಗಿ ಬಿಸಿಯಾಗುವುದು ಸಾಮಾನ್ಯ ಸಮಸ್ಯೆಯಾಗಿದ್ದು, ಇದು ರುಬ್ಬುವ ಚಕ್ರ ಮತ್ತು ವರ್ಕ್ಪೀಸ್ ಎರಡರ ಕಾರ್ಯಕ್ಷಮತೆಯ ಮೇಲೆ ಪರಿಣಾಮ ಬೀರುತ್ತದೆ. ಅತಿಯಾದ ಶಾಖವು ಚಕ್ರದ ಜೀವಿತಾವಧಿಯನ್ನು ಕಡಿಮೆ ಮಾಡುವುದು, ವರ್ಕ್ಪೀಸ್ಗೆ ಉಷ್ಣ ಹಾನಿ ಮತ್ತು ಒಟ್ಟಾರೆಯಾಗಿ ರುಬ್ಬುವ ದಕ್ಷತೆಯನ್ನು ಕಡಿಮೆ ಮಾಡುವುದು ಸೇರಿದಂತೆ ವಿವಿಧ ಸಮಸ್ಯೆಗಳಿಗೆ ಕಾರಣವಾಗಬಹುದು. ಅಧಿಕ ಬಿಸಿಯಾಗುವ ಸಮಸ್ಯೆಗಳನ್ನು ಪರಿಹರಿಸಲು ಸಂಭಾವ್ಯ ಕಾರಣಗಳು ಮತ್ತು ಪರಿಹಾರಗಳು ಇಲ್ಲಿವೆ:
ತಪ್ಪಾದ ಗ್ರೈಂಡಿಂಗ್ ನಿಯತಾಂಕಗಳು:
ಕಾರಣ:ಅತಿಯಾದ ವೇಗ, ಫೀಡ್ ದರ ಅಥವಾ ಕತ್ತರಿಸಿದ ಆಳದಂತಹ ಅನುಚಿತ ಗ್ರೈಂಡಿಂಗ್ ನಿಯತಾಂಕಗಳನ್ನು ಬಳಸುವುದರಿಂದ ಹೆಚ್ಚುವರಿ ಶಾಖವನ್ನು ಉತ್ಪಾದಿಸಬಹುದು.
ಪರಿಹಾರ:ಶಿಫಾರಸು ಮಾಡಲಾದ ವ್ಯಾಪ್ತಿಯಲ್ಲಿ ಗ್ರೈಂಡಿಂಗ್ ನಿಯತಾಂಕಗಳನ್ನು ಹೊಂದಿಸಿ. ರುಬ್ಬುವ ವಸ್ತುವನ್ನು ಆಧರಿಸಿ ಸೂಕ್ತ ಸೆಟ್ಟಿಂಗ್ಗಳಿಗಾಗಿ ತಯಾರಕರ ಮಾರ್ಗಸೂಚಿಗಳನ್ನು ನೋಡಿ.
ಅಸಮರ್ಪಕ ಕೂಲಿಂಗ್ ಅಥವಾ ಲೂಬ್ರಿಕೇಶನ್:
ಕಾರಣ:ಕೂಲಂಟ್ ಅಥವಾ ರುಬ್ಬುವ ದ್ರವದ ಸಾಕಷ್ಟು ಬಳಕೆಯು ಘರ್ಷಣೆ ಮತ್ತು ಶಾಖವನ್ನು ಹೆಚ್ಚಿಸಲು ಕಾರಣವಾಗಬಹುದು.
ಪರಿಹಾರ:ರುಬ್ಬುವ ಪ್ರಕ್ರಿಯೆಯಲ್ಲಿ ಕೂಲಂಟ್ ಅಥವಾ ಲೂಬ್ರಿಕಂಟ್ ಸಾಕಷ್ಟು ಪೂರೈಕೆಯಾಗುವಂತೆ ನೋಡಿಕೊಳ್ಳಿ. ಸರಿಯಾದ ಕೂಲಿಂಗ್ ಶಾಖವನ್ನು ಹೊರಹಾಕಲು ಸಹಾಯ ಮಾಡುತ್ತದೆ ಮತ್ತು ಉಷ್ಣ ಹಾನಿಯನ್ನು ತಡೆಯುತ್ತದೆ.
ತಪ್ಪಾದ ಚಕ್ರ ಆಯ್ಕೆ:
ಕಾರಣ:ರುಬ್ಬುವ ವಸ್ತುವಿಗೆ ಸೂಕ್ತವಲ್ಲದ ವಿಶೇಷಣಗಳೊಂದಿಗೆ ಗ್ರೈಂಡಿಂಗ್ ವೀಲ್ ಅನ್ನು ಆಯ್ಕೆ ಮಾಡುವುದರಿಂದ ಅಧಿಕ ಬಿಸಿಯಾಗಬಹುದು.
ಪರಿಹಾರ:ನಿರ್ದಿಷ್ಟ ಅನ್ವಯಕ್ಕೆ ಸರಿಯಾದ ಅಪಘರ್ಷಕ ಪ್ರಕಾರ, ಗ್ರಿಟ್ ಗಾತ್ರ ಮತ್ತು ಬಂಧದೊಂದಿಗೆ ಗ್ರೈಂಡಿಂಗ್ ಚಕ್ರವನ್ನು ಆಯ್ಕೆಮಾಡಿ. ಚಕ್ರವನ್ನು ವಸ್ತುಗಳಿಗೆ ಹೊಂದಿಸುವುದರಿಂದ ಶಾಖ ಉತ್ಪಾದನೆಯನ್ನು ಕಡಿಮೆ ಮಾಡುತ್ತದೆ.
ವರ್ಕ್ಪೀಸ್ ವಸ್ತುವಿನ ಸಮಸ್ಯೆಗಳು:
ಕಾರಣ:ಕೆಲವು ವಸ್ತುಗಳು, ವಿಶೇಷವಾಗಿ ಕಡಿಮೆ ಉಷ್ಣ ವಾಹಕತೆಯನ್ನು ಹೊಂದಿರುವ ವಸ್ತುಗಳು, ರುಬ್ಬುವ ಸಮಯದಲ್ಲಿ ಅಧಿಕ ಬಿಸಿಯಾಗುವ ಸಾಧ್ಯತೆ ಹೆಚ್ಚು.
ಪರಿಹಾರ:ಕಡಿಮೆ ಉಷ್ಣ ವಾಹಕತೆ ಹೊಂದಿರುವ ವಸ್ತುಗಳಿಗೆ ಗ್ರೈಂಡಿಂಗ್ ನಿಯತಾಂಕಗಳನ್ನು ಹೊಂದಿಸಿ. ಶಾಖ-ಸೂಕ್ಷ್ಮ ವಸ್ತುಗಳಿಗೆ ವಿನ್ಯಾಸಗೊಳಿಸಲಾದ ವಿಶೇಷ ಗ್ರೈಂಡಿಂಗ್ ಚಕ್ರವನ್ನು ಬಳಸುವುದನ್ನು ಪರಿಗಣಿಸಿ.
ವೀಲ್ ಡ್ರೆಸ್ಸಿಂಗ್ ಸಮಸ್ಯೆಗಳು:
ಕಾರಣ:ಗ್ರೈಂಡಿಂಗ್ ವೀಲ್ನ ಅಕ್ರಮಗಳು ಅಥವಾ ಅನುಚಿತ ಡ್ರೆಸ್ಸಿಂಗ್ ಅಸಮ ಸಂಪರ್ಕ ಮತ್ತು ಶಾಖದ ಶೇಖರಣೆಗೆ ಕಾರಣವಾಗಬಹುದು.
ಪರಿಹಾರ:ಗ್ರೈಂಡಿಂಗ್ ವೀಲ್ನ ಆಕಾರವನ್ನು ಕಾಪಾಡಿಕೊಳ್ಳಲು ಮತ್ತು ಯಾವುದೇ ಗ್ಲೇಜಿಂಗ್ ಅಥವಾ ಸಂಗ್ರಹವಾದ ಶಿಲಾಖಂಡರಾಶಿಗಳನ್ನು ತೆಗೆದುಹಾಕಲು ನಿಯಮಿತವಾಗಿ ಗ್ರೈಂಡಿಂಗ್ ವೀಲ್ ಅನ್ನು ಅಲಂಕರಿಸಿ. ಸರಿಯಾಗಿ ಧರಿಸಿರುವ ಚಕ್ರಗಳು ಸ್ಥಿರವಾದ ಗ್ರೈಂಡಿಂಗ್ ಕಾರ್ಯಕ್ಷಮತೆಯನ್ನು ಖಚಿತಪಡಿಸುತ್ತವೆ.
ಅಸಮರ್ಪಕ ಯಂತ್ರ ನಿರ್ವಹಣೆ:
ಕಾರಣ:ಸರಿಯಾಗಿ ನಿರ್ವಹಿಸದ ಗ್ರೈಂಡಿಂಗ್ ಯಂತ್ರಗಳು ಅಧಿಕ ಬಿಸಿಯಾಗುವಿಕೆಯ ಸಮಸ್ಯೆಗಳಿಗೆ ಕಾರಣವಾಗಬಹುದು.
ಪರಿಹಾರ:ಕೂಲಂಟ್ ವ್ಯವಸ್ಥೆಗಳನ್ನು ಪರಿಶೀಲಿಸುವುದು, ವೀಲ್ ಡ್ರೆಸ್ಸಿಂಗ್ ಉಪಕರಣಗಳನ್ನು ಪರಿಶೀಲಿಸುವುದು ಮತ್ತು ಸರಿಯಾದ ಜೋಡಣೆಯನ್ನು ಖಚಿತಪಡಿಸಿಕೊಳ್ಳುವುದು ಸೇರಿದಂತೆ ಗ್ರೈಂಡಿಂಗ್ ಯಂತ್ರದ ನಿಯಮಿತ ನಿರ್ವಹಣೆಯನ್ನು ಕೈಗೊಳ್ಳಿ. ಯಾವುದೇ ಯಾಂತ್ರಿಕ ಸಮಸ್ಯೆಗಳನ್ನು ತಕ್ಷಣ ಪರಿಹರಿಸಿ.
ವೀಲ್ ಕೂಲಂಟ್ ಹರಿವು ಸಾಕಷ್ಟಿಲ್ಲ:
ಕಾರಣ:ರುಬ್ಬುವ ವಲಯಕ್ಕೆ ಶೀತಕದ ಹರಿವು ಅಸಮರ್ಪಕವಾಗಿದ್ದರೆ, ಶಾಖದ ಹರಡುವಿಕೆ ಕಡಿಮೆಯಾಗಬಹುದು.
ಪರಿಹಾರ:ಕೂಲಂಟ್ ವಿತರಣಾ ವ್ಯವಸ್ಥೆಯನ್ನು ಪರಿಶೀಲಿಸಿ ಮತ್ತು ಅತ್ಯುತ್ತಮಗೊಳಿಸಿ. ಕೂಲಿಂಗ್ ದಕ್ಷತೆಯನ್ನು ಕಾಪಾಡಿಕೊಳ್ಳಲು ಕೂಲಂಟ್ ಪರಿಣಾಮಕಾರಿಯಾಗಿ ಗ್ರೈಂಡಿಂಗ್ ವಲಯವನ್ನು ತಲುಪುತ್ತದೆ ಎಂದು ಖಚಿತಪಡಿಸಿಕೊಳ್ಳಿ.
ಅತಿಯಾದ ರುಬ್ಬುವ ಸಮಯ:
ಕಾರಣ:ವಿರಾಮವಿಲ್ಲದೆ ದೀರ್ಘಕಾಲದವರೆಗೆ ರುಬ್ಬುವ ಅವಧಿಗಳು ಶಾಖದ ಶೇಖರಣೆಗೆ ಕಾರಣವಾಗಬಹುದು.
ಪರಿಹಾರ:ಅತಿಯಾದ ಶಾಖ ಸಂಗ್ರಹವನ್ನು ತಡೆಗಟ್ಟಲು ಮಧ್ಯಂತರ ರುಬ್ಬುವಿಕೆಯನ್ನು ಕಾರ್ಯಗತಗೊಳಿಸಿ ಮತ್ತು ವಿರಾಮಗಳನ್ನು ಅನುಮತಿಸಿ. ಈ ವಿಧಾನವು ದೊಡ್ಡ ಅಥವಾ ಸವಾಲಿನ ರುಬ್ಬುವ ಕಾರ್ಯಗಳಿಗೆ ವಿಶೇಷವಾಗಿ ಮುಖ್ಯವಾಗಿದೆ.
ಗ್ರೈಂಡಿಂಗ್ನಲ್ಲಿ ಅಧಿಕ ಬಿಸಿಯಾಗುವ ಸಮಸ್ಯೆಗಳನ್ನು ಪರಿಹರಿಸಲು ಸರಿಯಾದ ಸಲಕರಣೆಗಳ ಸೆಟಪ್, ಸೂಕ್ತವಾದ ಗ್ರೈಂಡಿಂಗ್ ನಿಯತಾಂಕಗಳು ಮತ್ತು ನಿಯಮಿತ ನಿರ್ವಹಣಾ ಅಭ್ಯಾಸಗಳನ್ನು ಒಳಗೊಂಡ ಸಮಗ್ರ ವಿಧಾನದ ಅಗತ್ಯವಿದೆ. ಅತ್ಯುತ್ತಮ ಕಾರ್ಯಕ್ಷಮತೆ, ವಿಸ್ತೃತ ಉಪಕರಣದ ಜೀವಿತಾವಧಿ ಮತ್ತು ಉತ್ತಮ-ಗುಣಮಟ್ಟದ ಫಲಿತಾಂಶಗಳನ್ನು ಖಚಿತಪಡಿಸಿಕೊಳ್ಳಲು ನಿರ್ವಾಹಕರು ಗ್ರೈಂಡಿಂಗ್ ಪ್ರಕ್ರಿಯೆಯಲ್ಲಿ ಶಾಖ ಉತ್ಪಾದನೆಯನ್ನು ಮೇಲ್ವಿಚಾರಣೆ ಮಾಡಬೇಕು ಮತ್ತು ನಿಯಂತ್ರಿಸಬೇಕು.
ಕಂಪನದ ಕಾಳಜಿಗಳು
ರುಬ್ಬುವ ಕಾರ್ಯಾಚರಣೆಗಳ ಸಮಯದಲ್ಲಿ ಅತಿಯಾದ ಕಂಪನವು ವಿವಿಧ ಸಮಸ್ಯೆಗಳಿಗೆ ಕಾರಣವಾಗಬಹುದು, ಅವುಗಳಲ್ಲಿ ಮೇಲ್ಮೈ ಗುಣಮಟ್ಟ ಕಡಿಮೆಯಾಗುವುದು, ಉಪಕರಣಗಳ ಸವೆತ ಹೆಚ್ಚಾಗುವುದು ಮತ್ತು ರುಬ್ಬುವ ಯಂತ್ರಕ್ಕೆ ಸಂಭಾವ್ಯ ಹಾನಿಯಾಗುವುದು ಸೇರಿವೆ. ನಿಖರ ಮತ್ತು ಪರಿಣಾಮಕಾರಿ ರುಬ್ಬುವ ಪ್ರಕ್ರಿಯೆಗಳನ್ನು ಸಾಧಿಸಲು ಕಂಪನದ ಕಾಳಜಿಗಳನ್ನು ಪರಿಹರಿಸುವುದು ಬಹಳ ಮುಖ್ಯ. ಕಂಪನ ಸಮಸ್ಯೆಗಳನ್ನು ತಗ್ಗಿಸಲು ಸಂಭಾವ್ಯ ಕಾರಣಗಳು ಮತ್ತು ಪರಿಹಾರಗಳು ಇಲ್ಲಿವೆ:
ಅಸಮ ಚಕ್ರ ಉಡುಗೆ:
ಕಾರಣ:ಗ್ರೈಂಡಿಂಗ್ ಚಕ್ರದ ಮೇಲೆ ಅನಿಯಮಿತ ಸವೆತವು ವರ್ಕ್ಪೀಸ್ನೊಂದಿಗೆ ಅಸಮ ಸಂಪರ್ಕಕ್ಕೆ ಕಾರಣವಾಗಬಹುದು, ಇದು ಕಂಪನಗಳಿಗೆ ಕಾರಣವಾಗಬಹುದು.
ಪರಿಹಾರ:ಸ್ಥಿರ ಮತ್ತು ಸಮತಟ್ಟಾದ ಮೇಲ್ಮೈಯನ್ನು ಕಾಪಾಡಿಕೊಳ್ಳಲು ಗ್ರೈಂಡಿಂಗ್ ವೀಲ್ ಅನ್ನು ನಿಯಮಿತವಾಗಿ ಪರೀಕ್ಷಿಸಿ ಮತ್ತು ಡ್ರೆಸ್ ಮಾಡಿ. ಸರಿಯಾದ ಚಕ್ರ ನಿರ್ವಹಣೆ ಕಂಪನಗಳನ್ನು ಕಡಿಮೆ ಮಾಡಲು ಸಹಾಯ ಮಾಡುತ್ತದೆ.
ಅಸಮತೋಲಿತ ಗ್ರೈಂಡಿಂಗ್ ವೀಲ್:
ಕಾರಣ:ಗ್ರೈಂಡಿಂಗ್ ಚಕ್ರದಲ್ಲಿನ ಅಸಮತೋಲನವು, ಅಸಮವಾದ ಉಡುಗೆ ಅಥವಾ ಉತ್ಪಾದನಾ ದೋಷಗಳಿಂದಾಗಿ, ಕಂಪನಕ್ಕೆ ಕಾರಣವಾಗಬಹುದು.
ಪರಿಹಾರ:ವೀಲ್ ಬ್ಯಾಲೆನ್ಸರ್ ಬಳಸಿ ಗ್ರೈಂಡಿಂಗ್ ವೀಲ್ ಅನ್ನು ಸಮತೋಲನಗೊಳಿಸಿ. ಸಮತೋಲನವು ತೂಕದ ಸಮನಾದ ವಿತರಣೆಯನ್ನು ಖಚಿತಪಡಿಸುತ್ತದೆ ಮತ್ತು ಕಾರ್ಯಾಚರಣೆಯ ಸಮಯದಲ್ಲಿ ಕಂಪನಗಳನ್ನು ಕಡಿಮೆ ಮಾಡುತ್ತದೆ.
ಅಸಮರ್ಪಕ ಯಂತ್ರ ಮಾಪನಾಂಕ ನಿರ್ಣಯ:
ಕಾರಣ:ಚಕ್ರ ಸ್ಪಿಂಡಲ್ ಅಥವಾ ವರ್ಕ್ಟೇಬಲ್ನಂತಹ ಯಂತ್ರದ ಘಟಕಗಳ ಕಳಪೆ ಮಾಪನಾಂಕ ನಿರ್ಣಯ ಅಥವಾ ತಪ್ಪು ಜೋಡಣೆಯು ಕಂಪನಗಳಿಗೆ ಕಾರಣವಾಗಬಹುದು.
ಪರಿಹಾರ:ಸರಿಯಾದ ಕಾರ್ಯವನ್ನು ಖಚಿತಪಡಿಸಿಕೊಳ್ಳಲು ಯಂತ್ರದ ಘಟಕಗಳನ್ನು ನಿಯಮಿತವಾಗಿ ಮಾಪನಾಂಕ ನಿರ್ಣಯಿಸಿ ಮತ್ತು ಜೋಡಿಸಿ. ಯಂತ್ರದ ಸೆಟಪ್ ಮತ್ತು ಜೋಡಣೆಗಾಗಿ ತಯಾರಕರ ಮಾರ್ಗಸೂಚಿಗಳನ್ನು ಅನುಸರಿಸಿ.
ಕೆಲಸದ ತುಣುಕು ಅಸಮತೋಲನ:
ಕಾರಣ:ಅಸಮ ಅಥವಾ ಸರಿಯಾಗಿ ಸುರಕ್ಷಿತವಲ್ಲದ ವರ್ಕ್ಪೀಸ್ ಅಸಮತೋಲನವನ್ನು ಉಂಟುಮಾಡಬಹುದು ಮತ್ತು ಕಂಪನಗಳನ್ನು ಉಂಟುಮಾಡಬಹುದು.
ಪರಿಹಾರ:ವರ್ಕ್ಪೀಸ್ ಅನ್ನು ಸರಿಯಾಗಿ ಸುರಕ್ಷಿತಗೊಳಿಸಿ, ಅದು ಸಮವಾಗಿ ಇರಿಸಲ್ಪಟ್ಟಿದೆ ಮತ್ತು ಕ್ಲ್ಯಾಂಪ್ ಆಗಿದೆಯೆ ಎಂದು ಖಚಿತಪಡಿಸಿಕೊಳ್ಳಿ. ಗ್ರೈಂಡಿಂಗ್ ಪ್ರಕ್ರಿಯೆಯನ್ನು ಪ್ರಾರಂಭಿಸುವ ಮೊದಲು ಯಾವುದೇ ಅಸಮತೋಲನ ಸಮಸ್ಯೆಗಳನ್ನು ಪರಿಹರಿಸಿ.
ತಪ್ಪಾದ ಚಕ್ರ ಆಯ್ಕೆ:
ಕಾರಣ:ಸೂಕ್ತವಲ್ಲದ ವಿಶೇಷಣಗಳೊಂದಿಗೆ ಗ್ರೈಂಡಿಂಗ್ ವೀಲ್ ಅನ್ನು ಬಳಸುವುದರಿಂದ ಕಂಪನಗಳು ಉಂಟಾಗಬಹುದು.
ಪರಿಹಾರ:ರುಬ್ಬುವ ವಸ್ತುವಿಗೆ ಸರಿಯಾದ ಅಪಘರ್ಷಕ ಪ್ರಕಾರ, ಧಾನ್ಯದ ಗಾತ್ರ ಮತ್ತು ಬಂಧವನ್ನು ಹೊಂದಿರುವ ಗ್ರೈಂಡಿಂಗ್ ಚಕ್ರವನ್ನು ಆಯ್ಕೆಮಾಡಿ. ಅಪ್ಲಿಕೇಶನ್ಗೆ ಚಕ್ರವನ್ನು ಹೊಂದಿಸುವುದರಿಂದ ಕಂಪನಗಳನ್ನು ಕಡಿಮೆ ಮಾಡುತ್ತದೆ.
ಯಂತ್ರ ಸವೆತ ಮತ್ತು ಹರಿದು ಹೋಗುವಿಕೆ:
ಕಾರಣ:ಬೇರಿಂಗ್ಗಳು ಅಥವಾ ಸ್ಪಿಂಡಲ್ಗಳಂತಹ ಹಳೆಯ ಅಥವಾ ಹಾನಿಗೊಳಗಾದ ಯಂತ್ರ ಘಟಕಗಳು ಕಂಪನಗಳಿಗೆ ಕಾರಣವಾಗಬಹುದು.
ಪರಿಹಾರ:ಸವೆದ ಯಂತ್ರದ ಭಾಗಗಳನ್ನು ನಿಯಮಿತವಾಗಿ ಪರಿಶೀಲಿಸಿ ಮತ್ತು ಬದಲಾಯಿಸಿ. ಸರಿಯಾದ ನಿರ್ವಹಣೆಯು ಅತಿಯಾದ ಕಂಪನಗಳನ್ನು ತಡೆಯಲು ಸಹಾಯ ಮಾಡುತ್ತದೆ ಮತ್ತು ಗ್ರೈಂಡಿಂಗ್ ಯಂತ್ರದ ಜೀವಿತಾವಧಿಯನ್ನು ಹೆಚ್ಚಿಸುತ್ತದೆ.
ಅಸಮರ್ಪಕ ಶೀತಕ ಹರಿವು:
ಕಾರಣ:ಗ್ರೈಂಡಿಂಗ್ ವಲಯಕ್ಕೆ ಸಾಕಷ್ಟು ಶೀತಕದ ಹರಿವು ಇಲ್ಲದಿರುವುದು ಶಾಖದ ಶೇಖರಣೆ ಮತ್ತು ಕಂಪನಗಳಿಗೆ ಕಾರಣವಾಗಬಹುದು.
ಪರಿಹಾರ:ಸರಿಯಾದ ತಂಪಾಗಿಸುವಿಕೆಯನ್ನು ಖಚಿತಪಡಿಸಿಕೊಳ್ಳಲು ಕೂಲಂಟ್ ವಿತರಣಾ ವ್ಯವಸ್ಥೆಯನ್ನು ಅತ್ಯುತ್ತಮಗೊಳಿಸಿ. ಪರಿಣಾಮಕಾರಿ ಕೂಲಿಂಗ್ ಉಷ್ಣ ವಿಸ್ತರಣೆ ಮತ್ತು ಸಂಕೋಚನದ ಅಪಾಯವನ್ನು ಕಡಿಮೆ ಮಾಡುತ್ತದೆ, ಇದು ಕಂಪನಗಳಿಗೆ ಕಾರಣವಾಗಬಹುದು.
ಪರಿಕರ ಹೋಲ್ಡರ್ ಸಮಸ್ಯೆಗಳು:
ಕಾರಣ:ಟೂಲ್ ಹೋಲ್ಡರ್ ಅಥವಾ ಸ್ಪಿಂಡಲ್ ಇಂಟರ್ಫೇಸ್ನಲ್ಲಿನ ಸಮಸ್ಯೆಗಳು ಕಂಪನಗಳನ್ನು ಉಂಟುಮಾಡಬಹುದು.
ಪರಿಹಾರ:ಟೂಲ್ ಹೋಲ್ಡರ್ ಅನ್ನು ಸುರಕ್ಷಿತವಾಗಿ ಜೋಡಿಸಲಾಗಿದೆ ಮತ್ತು ಸ್ಪಿಂಡಲ್ನೊಂದಿಗೆ ಸರಿಯಾಗಿ ಜೋಡಿಸಲಾಗಿದೆ ಎಂದು ಖಚಿತಪಡಿಸಿಕೊಳ್ಳಿ. ಕಂಪನಗಳನ್ನು ಕಡಿಮೆ ಮಾಡಲು ಉತ್ತಮ ಗುಣಮಟ್ಟದ ಮತ್ತು ಸರಿಯಾಗಿ ನಿರ್ವಹಿಸಲಾದ ಟೂಲ್ ಹೋಲ್ಡರ್ಗಳನ್ನು ಬಳಸಿ.
ಯಂತ್ರ ಅಡಿಪಾಯ:
ಕಾರಣ:ಯಂತ್ರದ ಕಳಪೆ ಅಡಿಪಾಯ ಅಥವಾ ಅಸಮರ್ಪಕ ಬೆಂಬಲವು ಕಂಪನಗಳನ್ನು ವರ್ಧಿಸಬಹುದು.
ಪರಿಹಾರ:ಗ್ರೈಂಡಿಂಗ್ ಯಂತ್ರವನ್ನು ಸ್ಥಿರ ಮತ್ತು ಸರಿಯಾಗಿ ವಿನ್ಯಾಸಗೊಳಿಸಲಾದ ಅಡಿಪಾಯದ ಮೇಲೆ ಸ್ಥಾಪಿಸಲಾಗಿದೆ ಎಂದು ಖಚಿತಪಡಿಸಿಕೊಳ್ಳಿ. ಯಂತ್ರಕ್ಕೆ ಹರಡುವ ಕಂಪನಗಳನ್ನು ಕಡಿಮೆ ಮಾಡಲು ಯಾವುದೇ ರಚನಾತ್ಮಕ ಸಮಸ್ಯೆಗಳನ್ನು ಪರಿಹರಿಸಿ.
ಗ್ರೈಂಡಿಂಗ್ನಲ್ಲಿ ಕಂಪನದ ಕಾಳಜಿಗಳನ್ನು ಪರಿಣಾಮಕಾರಿಯಾಗಿ ಪರಿಹರಿಸಲು ಸರಿಯಾದ ಯಂತ್ರ ನಿರ್ವಹಣೆ, ಚಕ್ರ ಆಯ್ಕೆ ಮತ್ತು ವರ್ಕ್ಪೀಸ್ ನಿರ್ವಹಣೆಯ ಸಂಯೋಜನೆಯ ಅಗತ್ಯವಿದೆ. ನಿರ್ವಾಹಕರು ಸಮಸ್ಯೆಗಳನ್ನು ಗುರುತಿಸಲು ಮತ್ತು ತ್ವರಿತವಾಗಿ ಪರಿಹರಿಸಲು ನಿಯಮಿತ ತಪಾಸಣೆ ಮತ್ತು ನಿರ್ವಹಣಾ ಅಭ್ಯಾಸಗಳನ್ನು ಜಾರಿಗೆ ತರಬೇಕು, ಇದರಿಂದಾಗಿ ಸುಧಾರಿತ ಗ್ರೈಂಡಿಂಗ್ ಕಾರ್ಯಕ್ಷಮತೆ ಮತ್ತು ಗುಣಮಟ್ಟ ಉಂಟಾಗುತ್ತದೆ.
ಗ್ರೈಂಡಿಂಗ್ನಲ್ಲಿ ಲೋಡ್ ಸಮಸ್ಯೆಗಳು
ರುಬ್ಬುವಾಗ ಲೋಡಿಂಗ್ ಎಂದರೆ ರುಬ್ಬುವ ಚಕ್ರದ ಮೇಲಿನ ಅಪಘರ್ಷಕ ಧಾನ್ಯಗಳ ನಡುವಿನ ಸ್ಥಳಗಳು ರುಬ್ಬುವ ವಸ್ತುಗಳಿಂದ ತುಂಬಿ, ಕತ್ತರಿಸುವ ಕ್ರಿಯೆ ಕಡಿಮೆಯಾಗಲು ಮತ್ತು ಘರ್ಷಣೆ ಹೆಚ್ಚಾಗಲು ಕಾರಣವಾಗುವ ವಿದ್ಯಮಾನ. ಲೋಡಿಂಗ್ ರುಬ್ಬುವ ಪ್ರಕ್ರಿಯೆಯ ದಕ್ಷತೆ ಮತ್ತು ಗುಣಮಟ್ಟದ ಮೇಲೆ ನಕಾರಾತ್ಮಕ ಪರಿಣಾಮ ಬೀರುತ್ತದೆ. ಲೋಡಿಂಗ್ ಸಮಸ್ಯೆಗಳನ್ನು ಪರಿಹರಿಸಲು ಸಂಭಾವ್ಯ ಕಾರಣಗಳು ಮತ್ತು ಪರಿಹಾರಗಳು ಇಲ್ಲಿವೆ:
ಮೃದುವಾದ ವರ್ಕ್ಪೀಸ್ ವಸ್ತು:
ಕಾರಣ:ಮೃದುವಾದ ವಸ್ತುಗಳನ್ನು ರುಬ್ಬುವುದರಿಂದ ಅಪಘರ್ಷಕ ಧಾನ್ಯಗಳು ಬೇಗನೆ ಮುಚ್ಚಿಹೋಗಬಹುದು.
ಪರಿಹಾರ:ಮೃದುವಾದ ವಸ್ತುಗಳ ಮೇಲೆ ಕೆಲಸ ಮಾಡುವಾಗ ಒರಟಾದ ಗ್ರಿಟ್ ಮತ್ತು ತೆರೆದ ರಚನೆಯನ್ನು ಹೊಂದಿರುವ ಗ್ರೈಂಡಿಂಗ್ ವೀಲ್ ಅನ್ನು ಬಳಸಿ. ಇದು ತ್ವರಿತ ಲೋಡಿಂಗ್ ಅನ್ನು ತಡೆಯಲು ಸಹಾಯ ಮಾಡುತ್ತದೆ ಮತ್ತು ಪರಿಣಾಮಕಾರಿ ಚಿಪ್ ತೆಗೆಯಲು ಅನುವು ಮಾಡಿಕೊಡುತ್ತದೆ.
ವಸ್ತು ಮಾಲಿನ್ಯ:
ಕಾರಣ:ಎಣ್ಣೆಗಳು, ಗ್ರೀಸ್ ಅಥವಾ ಶೀತಕದ ಅವಶೇಷಗಳಂತಹ ವರ್ಕ್ಪೀಸ್ ವಸ್ತುವಿನಲ್ಲಿರುವ ಮಾಲಿನ್ಯಕಾರಕಗಳು ಲೋಡ್ ಆಗಲು ಕಾರಣವಾಗಬಹುದು.
ಪರಿಹಾರ:ಮಾಲಿನ್ಯಕಾರಕಗಳನ್ನು ತೆಗೆದುಹಾಕಲು ರುಬ್ಬುವ ಮೊದಲು ವರ್ಕ್ಪೀಸ್ ಅನ್ನು ಸರಿಯಾಗಿ ಸ್ವಚ್ಛಗೊಳಿಸುವುದನ್ನು ಖಚಿತಪಡಿಸಿಕೊಳ್ಳಿ. ಲೋಡ್ ಮಾಡುವುದನ್ನು ಕಡಿಮೆ ಮಾಡಲು ಸೂಕ್ತವಾದ ಕತ್ತರಿಸುವ ದ್ರವಗಳು ಅಥವಾ ಶೀತಕಗಳನ್ನು ಬಳಸಿ.
ತಪ್ಪಾದ ಕೂಲಂಟ್ ಅಪ್ಲಿಕೇಶನ್:
ಕಾರಣ:ಕೂಲಂಟ್ನ ಅಸಮರ್ಪಕ ಅಥವಾ ಅನುಚಿತ ಅನ್ವಯವು ಸಾಕಷ್ಟು ನಯಗೊಳಿಸುವಿಕೆ ಮತ್ತು ತಂಪಾಗಿಸುವಿಕೆಗೆ ಕಾರಣವಾಗಬಹುದು, ಇದು ಲೋಡಿಂಗ್ಗೆ ಕಾರಣವಾಗುತ್ತದೆ.
ಪರಿಹಾರ:ಕೂಲಂಟ್ ಹರಿವು ಮತ್ತು ಸಾಂದ್ರತೆಯನ್ನು ಅತ್ಯುತ್ತಮಗೊಳಿಸಿ. ಕೂಲಂಟ್ ಪರಿಣಾಮಕಾರಿಯಾಗಿ ಗ್ರೈಂಡಿಂಗ್ ವಲಯವನ್ನು ತಲುಪಿ ಪ್ರಕ್ರಿಯೆಯನ್ನು ನಯಗೊಳಿಸಿ ತಂಪಾಗಿಸಿ, ಲೋಡ್ ಆಗುವುದನ್ನು ತಡೆಯುತ್ತದೆ ಎಂದು ಖಚಿತಪಡಿಸಿಕೊಳ್ಳಿ.
ಚಕ್ರದ ತೀಕ್ಷ್ಣತೆ ಸಾಕಷ್ಟಿಲ್ಲ:
ಕಾರಣ:ಮಂದ ಅಥವಾ ಸವೆದ ಗ್ರೈಂಡಿಂಗ್ ಚಕ್ರಗಳು ತಮ್ಮ ಕತ್ತರಿಸುವ ದಕ್ಷತೆಯನ್ನು ಕಳೆದುಕೊಳ್ಳುವುದರಿಂದ ಲೋಡ್ ಆಗುವ ಸಾಧ್ಯತೆ ಹೆಚ್ಚು.
ಪರಿಹಾರ:ಗ್ರೈಂಡಿಂಗ್ ವೀಲ್ನ ತೀಕ್ಷ್ಣತೆಯನ್ನು ಕಾಪಾಡಿಕೊಳ್ಳಲು ಅದನ್ನು ನಿಯಮಿತವಾಗಿ ಡ್ರೆಸ್ ಮಾಡಿ ಮತ್ತು ಹರಿತಗೊಳಿಸಿ. ತಾಜಾ ಅಪಘರ್ಷಕ ಧಾನ್ಯಗಳನ್ನು ಬಹಿರಂಗಪಡಿಸಲು ಮತ್ತು ಕತ್ತರಿಸುವ ಕ್ರಿಯೆಯನ್ನು ಹೆಚ್ಚಿಸಲು ವೀಲ್ ಡ್ರೆಸ್ಸರ್ ಬಳಸಿ.
ಕಡಿಮೆ ಚಕ್ರ ವೇಗ:
ಕಾರಣ:ಕಡಿಮೆ ವೇಗದಲ್ಲಿ ಗ್ರೈಂಡಿಂಗ್ ವೀಲ್ ಅನ್ನು ನಿರ್ವಹಿಸುವುದರಿಂದ ಚಿಪ್ಗಳನ್ನು ಹೊರಹಾಕಲು ಸಾಕಷ್ಟು ಕೇಂದ್ರಾಪಗಾಮಿ ಬಲವನ್ನು ಒದಗಿಸದಿರಬಹುದು, ಇದು ಲೋಡಿಂಗ್ಗೆ ಕಾರಣವಾಗುತ್ತದೆ.
ಪರಿಹಾರ:ನಿರ್ದಿಷ್ಟ ಚಕ್ರ ಮತ್ತು ವರ್ಕ್ಪೀಸ್ ಸಂಯೋಜನೆಗೆ ಶಿಫಾರಸು ಮಾಡಲಾದ ವೇಗದಲ್ಲಿ ಗ್ರೈಂಡಿಂಗ್ ಯಂತ್ರವು ಕಾರ್ಯನಿರ್ವಹಿಸುತ್ತದೆ ಎಂದು ಖಚಿತಪಡಿಸಿಕೊಳ್ಳಿ. ಹೆಚ್ಚಿನ ವೇಗವು ಉತ್ತಮ ಚಿಪ್ ತೆಗೆಯುವಿಕೆಗೆ ಸಹಾಯ ಮಾಡುತ್ತದೆ.
ಅತಿಯಾದ ಒತ್ತಡ:
ಕಾರಣ:ರುಬ್ಬುವ ಸಮಯದಲ್ಲಿ ಹೆಚ್ಚು ಒತ್ತಡ ಹೇರುವುದರಿಂದ ವಸ್ತುವು ಚಕ್ರದೊಳಗೆ ಬಲವಂತವಾಗಿ ಸಿಲುಕಿ, ಲೋಡಿಂಗ್ಗೆ ಕಾರಣವಾಗಬಹುದು.
ಪರಿಹಾರ:ಮಧ್ಯಮ ಮತ್ತು ಸ್ಥಿರವಾದ ಗ್ರೈಂಡಿಂಗ್ ಒತ್ತಡವನ್ನು ಬಳಸಿ. ಲೋಡ್ಗೆ ಕಾರಣವಾಗುವ ಅತಿಯಾದ ಒತ್ತಡವಿಲ್ಲದೆ ಚಕ್ರವು ಪರಿಣಾಮಕಾರಿಯಾಗಿ ಕತ್ತರಿಸಲು ಅನುವು ಮಾಡಿಕೊಡಲು ಫೀಡ್ ದರವನ್ನು ಹೊಂದಿಸಿ.
ತಪ್ಪಾದ ಚಕ್ರ ವಿಶೇಷಣಗಳು:
ಕಾರಣ:ರುಬ್ಬುವ ವಸ್ತುವಿಗೆ ತಪ್ಪಾದ ವಿಶೇಷಣಗಳೊಂದಿಗೆ ಗ್ರೈಂಡಿಂಗ್ ಚಕ್ರವನ್ನು ಬಳಸುವುದರಿಂದ ಲೋಡಿಂಗ್ ಉಂಟಾಗಬಹುದು.
ಪರಿಹಾರ:ನಿರ್ದಿಷ್ಟ ಅನ್ವಯಕ್ಕೆ ಸೂಕ್ತವಾದ ಅಪಘರ್ಷಕ ಪ್ರಕಾರ, ಗ್ರಿಟ್ ಗಾತ್ರ ಮತ್ತು ಬಂಧದೊಂದಿಗೆ ಗ್ರೈಂಡಿಂಗ್ ಚಕ್ರವನ್ನು ಆಯ್ಕೆಮಾಡಿ. ಚಕ್ರವನ್ನು ವಸ್ತುಗಳಿಗೆ ಹೊಂದಿಸುವುದು ಲೋಡ್ ಆಗುವುದನ್ನು ತಡೆಯಲು ಸಹಾಯ ಮಾಡುತ್ತದೆ.
ಅಸಮರ್ಪಕ ಶೀತಕ ಶುಚಿಗೊಳಿಸುವಿಕೆ:
ಕಾರಣ:ಕಲುಷಿತ ಅಥವಾ ಹಳೆಯ ಕೂಲಂಟ್ ಲೋಡಿಂಗ್ ಸಮಸ್ಯೆಗಳಿಗೆ ಕಾರಣವಾಗಬಹುದು.
ಪರಿಹಾರ:ಮಾಲಿನ್ಯಕಾರಕಗಳು ಸಂಗ್ರಹವಾಗುವುದನ್ನು ತಡೆಯಲು ನಿಯಮಿತವಾಗಿ ಕೂಲಂಟ್ ಅನ್ನು ಸ್ವಚ್ಛಗೊಳಿಸಿ ಮತ್ತು ಬದಲಾಯಿಸಿ. ತಾಜಾ ಮತ್ತು ಶುದ್ಧ ಕೂಲಂಟ್ ನಯಗೊಳಿಸುವಿಕೆ ಮತ್ತು ತಂಪಾಗಿಸುವಿಕೆಯನ್ನು ಹೆಚ್ಚಿಸುತ್ತದೆ, ಲೋಡ್ ಆಗುವ ಸಾಧ್ಯತೆಯನ್ನು ಕಡಿಮೆ ಮಾಡುತ್ತದೆ.
ಅನುಚಿತ ಡ್ರೆಸ್ಸಿಂಗ್ ತಂತ್ರ:
ಕಾರಣ:ಗ್ರೈಂಡಿಂಗ್ ಚಕ್ರದ ತಪ್ಪಾದ ಡ್ರೆಸ್ಸಿಂಗ್ ಅಕ್ರಮಗಳು ಮತ್ತು ಲೋಡಿಂಗ್ಗೆ ಕಾರಣವಾಗಬಹುದು.
ಪರಿಹಾರ:ಸೂಕ್ತವಾದ ಡ್ರೆಸ್ಸಿಂಗ್ ಉಪಕರಣವನ್ನು ಬಳಸಿಕೊಂಡು ಚಕ್ರವನ್ನು ಸರಿಯಾಗಿ ಧರಿಸಿ. ಲೋಡ್ ಆಗುವುದನ್ನು ತಡೆಯಲು ಚಕ್ರದ ಪ್ರೊಫೈಲ್ ಸ್ಥಿರವಾಗಿದೆ ಮತ್ತು ಅಕ್ರಮಗಳಿಂದ ಮುಕ್ತವಾಗಿದೆ ಎಂದು ಖಚಿತಪಡಿಸಿಕೊಳ್ಳಿ.
ಲೋಡಿಂಗ್ ಸಮಸ್ಯೆಗಳನ್ನು ಪರಿಣಾಮಕಾರಿಯಾಗಿ ಪರಿಹರಿಸುವುದು ಸರಿಯಾದ ಚಕ್ರ ಆಯ್ಕೆ, ಯಂತ್ರ ಸೆಟಪ್ ಮತ್ತು ನಿರ್ವಹಣಾ ಅಭ್ಯಾಸಗಳ ಸಂಯೋಜನೆಯನ್ನು ಒಳಗೊಂಡಿರುತ್ತದೆ. ನಿರ್ವಾಹಕರು ಶಿಫಾರಸು ಮಾಡಿದ ಕಾರ್ಯವಿಧಾನಗಳನ್ನು ಅನುಸರಿಸಬೇಕು, ಸೂಕ್ತವಾದ ಗ್ರೈಂಡಿಂಗ್ ನಿಯತಾಂಕಗಳನ್ನು ಬಳಸಬೇಕು ಮತ್ತು ಲೋಡಿಂಗ್ ಅನ್ನು ಕಡಿಮೆ ಮಾಡಲು ಮತ್ತು ಗ್ರೈಂಡಿಂಗ್ ಕಾರ್ಯಕ್ಷಮತೆಯನ್ನು ಅತ್ಯುತ್ತಮವಾಗಿಸಲು ನಿಯಮಿತ ಚಕ್ರ ಡ್ರೆಸ್ಸಿಂಗ್ ಅನ್ನು ಕಾರ್ಯಗತಗೊಳಿಸಬೇಕು.
ವಿವಿಧ ಲೋಹ ಕೆಲಸ ಮತ್ತು ತಯಾರಿಕೆ ಅನ್ವಯಿಕೆಗಳಲ್ಲಿ ಅತ್ಯುತ್ತಮ ಫಲಿತಾಂಶಗಳನ್ನು ಸಾಧಿಸಲು ಸರಿಯಾದ ಗ್ರೈಂಡಿಂಗ್ ಡಿಸ್ಕ್ ಅನ್ನು ಆಯ್ಕೆ ಮಾಡುವುದು ಬಹಳ ಮುಖ್ಯ. ಆಯ್ಕೆಯು ಕೆಲಸ ಮಾಡುತ್ತಿರುವ ವಸ್ತು, ಅಪೇಕ್ಷಿತ ಮುಕ್ತಾಯ ಮತ್ತು ಬಳಸುತ್ತಿರುವ ಗ್ರೈಂಡರ್ ಪ್ರಕಾರದಂತಹ ಅಂಶಗಳನ್ನು ಅವಲಂಬಿಸಿರುತ್ತದೆ.
ಸರಿಯಾದ ಗ್ರೈಂಡಿಂಗ್ ಡಿಸ್ಕ್ ಆಯ್ಕೆ
ವಸ್ತು ಹೊಂದಾಣಿಕೆ:
ಫೆರಸ್ ಲೋಹಗಳು (ಉಕ್ಕು, ಕಬ್ಬಿಣ):ಫೆರಸ್ ಲೋಹಗಳಿಗಾಗಿ ನಿರ್ದಿಷ್ಟವಾಗಿ ವಿನ್ಯಾಸಗೊಳಿಸಲಾದ ಗ್ರೈಂಡಿಂಗ್ ಡಿಸ್ಕ್ಗಳನ್ನು ಬಳಸಿ. ಈ ಡಿಸ್ಕ್ಗಳು ಸಾಮಾನ್ಯವಾಗಿ ಉಕ್ಕಿನ ಗಡಸುತನಕ್ಕೆ ಸೂಕ್ತವಾದ ಅಪಘರ್ಷಕಗಳನ್ನು ಹೊಂದಿರುತ್ತವೆ ಮತ್ತು ಲೋಡ್ ಆಗುವ ಸಾಧ್ಯತೆ ಕಡಿಮೆ.
ಕಬ್ಬಿಣವಲ್ಲದ ಲೋಹಗಳು (ಅಲ್ಯೂಮಿನಿಯಂ, ಹಿತ್ತಾಳೆ):ಮೃದುವಾದ ಲೋಹಗಳು ಅಡಚಣೆಯಾಗದಂತೆ ತಡೆಯಲು ಸೂಕ್ತವಾದ ಅಪಘರ್ಷಕಗಳನ್ನು ಹೊಂದಿರುವ ಡಿಸ್ಕ್ಗಳನ್ನು ಆರಿಸಿ. ಅಲ್ಯೂಮಿನಿಯಂ ಆಕ್ಸೈಡ್ ಅಥವಾ ಸಿಲಿಕಾನ್ ಕಾರ್ಬೈಡ್ ಡಿಸ್ಕ್ಗಳು ಸಾಮಾನ್ಯ ಆಯ್ಕೆಗಳಾಗಿವೆ.
ಸವೆತ ದ್ರವ್ಯ:
ಅಲ್ಯೂಮಿನಿಯಂ ಆಕ್ಸೈಡ್:ಫೆರಸ್ ಲೋಹಗಳ ಮೇಲೆ ಸಾಮಾನ್ಯ ಉದ್ದೇಶದ ರುಬ್ಬುವಿಕೆಗೆ ಸೂಕ್ತವಾಗಿದೆ. ಇದು ಬಾಳಿಕೆ ಬರುವ ಮತ್ತು ಬಹುಮುಖವಾಗಿದೆ.
ಜಿರ್ಕೋನಿಯಾ ಅಲ್ಯೂಮಿನಾ:ಹೆಚ್ಚಿನ ಕತ್ತರಿಸುವ ದಕ್ಷತೆ ಮತ್ತು ದೀರ್ಘಾಯುಷ್ಯವನ್ನು ನೀಡುತ್ತದೆ, ಇದು ಫೆರಸ್ ಮತ್ತು ನಾನ್-ಫೆರಸ್ ಲೋಹಗಳ ಮೇಲೆ ಆಕ್ರಮಣಕಾರಿ ಗ್ರೈಂಡಿಂಗ್ಗೆ ಸೂಕ್ತವಾಗಿದೆ.
ಸಿಲಿಕಾನ್ ಕಾರ್ಬೈಡ್:ಕಬ್ಬಿಣವಲ್ಲದ ಲೋಹಗಳು ಮತ್ತು ಕಲ್ಲುಗಳನ್ನು ರುಬ್ಬಲು ಸೂಕ್ತವಾಗಿದೆ. ಇದು ಅಲ್ಯೂಮಿನಿಯಂ ಆಕ್ಸೈಡ್ ಗಿಂತ ತೀಕ್ಷ್ಣವಾಗಿರುತ್ತದೆ ಆದರೆ ಕಡಿಮೆ ಬಾಳಿಕೆ ಬರುತ್ತದೆ.
ಗ್ರಿಟ್ ಗಾತ್ರ:
ಒರಟಾದ ಗ್ರಿಟ್ (24-36):ತ್ವರಿತ ಸ್ಟಾಕ್ ತೆಗೆಯುವಿಕೆ ಮತ್ತು ಭಾರೀ-ಡ್ಯೂಟಿ ಗ್ರೈಂಡಿಂಗ್.
ಮಧ್ಯಮ ಗ್ರಿಟ್ (40-60):ಸ್ಟಾಕ್ ತೆಗೆಯುವಿಕೆ ಮತ್ತು ಮೇಲ್ಮೈ ಮುಕ್ತಾಯವನ್ನು ಸಮತೋಲನಗೊಳಿಸುತ್ತದೆ.
ಫೈನ್ ಗ್ರಿಟ್ (80-120):ಮೇಲ್ಮೈ ತಯಾರಿಕೆ ಮತ್ತು ಲಘುವಾಗಿ ರುಬ್ಬಲು ಸೂಕ್ತವಾದ ನಯವಾದ ಮುಕ್ತಾಯವನ್ನು ಒದಗಿಸುತ್ತದೆ.
ಚಕ್ರದ ಪ್ರಕಾರ:
ವಿಧ 27 (ಖಿನ್ನತೆಯ ಕೇಂದ್ರ):ಸಮತಟ್ಟಾದ ಮೇಲ್ಮೈ ಹೊಂದಿರುವ ಪ್ರಮಾಣಿತ ಗ್ರೈಂಡಿಂಗ್ ಡಿಸ್ಕ್, ಮೇಲ್ಮೈ ಗ್ರೈಂಡಿಂಗ್ ಮತ್ತು ಅಂಚಿನ ಕೆಲಸಕ್ಕೆ ಸೂಕ್ತವಾಗಿದೆ.
ವಿಧ 29 (ಶಂಕುವಿನಾಕಾರದ):ಆಕ್ರಮಣಕಾರಿ ಸ್ಟಾಕ್ ತೆಗೆಯುವಿಕೆ ಮತ್ತು ಉತ್ತಮ ಮೇಲ್ಮೈ ಮಿಶ್ರಣಕ್ಕಾಗಿ ಕೋನೀಯ ವಿನ್ಯಾಸ.
ವಿಧ 1 (ನೇರ):ಕಟ್-ಆಫ್ ಅನ್ವಯಿಕೆಗಳಿಗೆ ಬಳಸಲಾಗುತ್ತದೆ. ನಿಖರವಾದ ಕತ್ತರಿಸುವಿಕೆಗಾಗಿ ಇದು ತೆಳುವಾದ ಪ್ರೊಫೈಲ್ ಅನ್ನು ಒದಗಿಸುತ್ತದೆ.
ಅಪ್ಲಿಕೇಶನ್:
ರುಬ್ಬುವುದು:ವಸ್ತು ತೆಗೆಯುವಿಕೆ ಮತ್ತು ಆಕಾರಕ್ಕಾಗಿ ಪ್ರಮಾಣಿತ ಗ್ರೈಂಡಿಂಗ್ ಡಿಸ್ಕ್ಗಳು.
ಕತ್ತರಿಸುವುದು:ಲೋಹವನ್ನು ಕತ್ತರಿಸಲು ಕಟ್-ಆಫ್ ಚಕ್ರಗಳನ್ನು ಬಳಸಿ, ನೇರ ಮತ್ತು ಸ್ವಚ್ಛವಾದ ಅಂಚನ್ನು ಒದಗಿಸಿ.
ಫ್ಲಾಪ್ ಡಿಸ್ಕ್ಗಳು:ರುಬ್ಬುವಿಕೆ ಮತ್ತು ಮುಗಿಸುವಿಕೆಯನ್ನು ಒಂದರಲ್ಲಿ ಸೇರಿಸಿ. ಮೇಲ್ಮೈಗಳನ್ನು ಮಿಶ್ರಣ ಮಾಡಲು ಮತ್ತು ಸುಗಮಗೊಳಿಸಲು ಸೂಕ್ತವಾಗಿದೆ.
ಗ್ರೈಂಡರ್ ಜೊತೆ ಹೊಂದಾಣಿಕೆ:
ಗ್ರೈಂಡಿಂಗ್ ಡಿಸ್ಕ್ ಬಳಸುತ್ತಿರುವ ಗ್ರೈಂಡರ್ನ ಪ್ರಕಾರ ಮತ್ತು ವೇಗಕ್ಕೆ ಹೊಂದಿಕೆಯಾಗುತ್ತದೆ ಎಂದು ಖಚಿತಪಡಿಸಿಕೊಳ್ಳಿ. ಡಿಸ್ಕ್ನ ಗರಿಷ್ಠ RPM (ಪ್ರತಿ ನಿಮಿಷಕ್ಕೆ ಕ್ರಾಂತಿಗಳು) ಗಾಗಿ ತಯಾರಕರ ಶಿಫಾರಸುಗಳನ್ನು ಪರಿಶೀಲಿಸಿ.
ಕಾರ್ಯದ ನಿರ್ದಿಷ್ಟತೆ:
ಭಾರೀ ದಾಸ್ತಾನು ತೆಗೆಯುವಿಕೆ:ಪರಿಣಾಮಕಾರಿ ವಸ್ತು ತೆಗೆಯುವಿಕೆಗಾಗಿ ಒರಟಾದ ಗ್ರಿಟ್ ಮತ್ತು ಟೈಪ್ 27 ಅಥವಾ ಟೈಪ್ 29 ಡಿಸ್ಕ್ ಅನ್ನು ಆರಿಸಿ.
ಮೇಲ್ಮೈ ಪೂರ್ಣಗೊಳಿಸುವಿಕೆ:ಮೃದುವಾದ ಮುಕ್ತಾಯಕ್ಕಾಗಿ ಫ್ಲಾಪ್ ಡಿಸ್ಕ್ಗಳೊಂದಿಗೆ ಮಧ್ಯಮದಿಂದ ಉತ್ತಮವಾದ ಧಾನ್ಯಗಳನ್ನು ಆರಿಸಿಕೊಳ್ಳಿ.
ಸುರಕ್ಷತಾ ಪರಿಗಣನೆಗಳು:
ಸುರಕ್ಷತಾ ಕನ್ನಡಕಗಳು ಮತ್ತು ಕೈಗವಸುಗಳಂತಹ ಸೂಕ್ತವಾದ ವೈಯಕ್ತಿಕ ರಕ್ಷಣಾ ಸಾಧನಗಳನ್ನು (ಪಿಪಿಇ) ಧರಿಸುವುದು ಸೇರಿದಂತೆ ಸುರಕ್ಷತಾ ಮಾರ್ಗಸೂಚಿಗಳನ್ನು ಅನುಸರಿಸಿ.
ಹೆಚ್ಚಿನ ಬಾಳಿಕೆ ಮತ್ತು ಸುರಕ್ಷತೆಗಾಗಿ ಬಲವರ್ಧಿತ ಡಿಸ್ಕ್ಗಳನ್ನು ಆರಿಸಿ.
ಬ್ರ್ಯಾಂಡ್ ಮತ್ತು ಗುಣಮಟ್ಟ:
ಗುಣಮಟ್ಟ ಮತ್ತು ಸ್ಥಿರತೆಗೆ ಹೆಸರುವಾಸಿಯಾದ ಪ್ರತಿಷ್ಠಿತ ಬ್ರ್ಯಾಂಡ್ಗಳಿಂದ ಡಿಸ್ಕ್ಗಳನ್ನು ಆಯ್ಕೆಮಾಡಿ. ಉತ್ತಮ ಗುಣಮಟ್ಟದ ಡಿಸ್ಕ್ಗಳು ಉತ್ತಮ ಕಾರ್ಯಕ್ಷಮತೆ ಮತ್ತು ಬಾಳಿಕೆಯನ್ನು ನೀಡುತ್ತವೆ.
ವೆಚ್ಚ ಪರಿಗಣನೆ:
ಆರಂಭಿಕ ವೆಚ್ಚವನ್ನು ಗ್ರೈಂಡಿಂಗ್ ಡಿಸ್ಕ್ನ ನಿರೀಕ್ಷಿತ ಜೀವಿತಾವಧಿ ಮತ್ತು ಕಾರ್ಯಕ್ಷಮತೆಯೊಂದಿಗೆ ಸಮತೋಲನಗೊಳಿಸಿ. ಉತ್ತಮ ಗುಣಮಟ್ಟದ ಡಿಸ್ಕ್ಗಳು ಹೆಚ್ಚಿನ ಮುಂಗಡ ವೆಚ್ಚವನ್ನು ಹೊಂದಿರಬಹುದು ಆದರೆ ಕಾಲಾನಂತರದಲ್ಲಿ ಉತ್ತಮ ಮೌಲ್ಯವನ್ನು ಒದಗಿಸಬಹುದು.
ಈ ಅಂಶಗಳನ್ನು ಪರಿಗಣಿಸುವ ಮೂಲಕ, ನಿರ್ವಾಹಕರು ತಮ್ಮ ನಿರ್ದಿಷ್ಟ ಅನ್ವಯಿಕೆಗಳಿಗೆ ಸರಿಯಾದ ಗ್ರೈಂಡಿಂಗ್ ಡಿಸ್ಕ್ ಅನ್ನು ಆಯ್ಕೆ ಮಾಡಬಹುದು, ದಕ್ಷತೆ, ಸುರಕ್ಷತೆ ಮತ್ತು ಅತ್ಯುತ್ತಮ ಫಲಿತಾಂಶಗಳನ್ನು ಖಚಿತಪಡಿಸಿಕೊಳ್ಳಬಹುದು.
ತೀರ್ಮಾನ
ಕೊನೆಯಲ್ಲಿ, ಸೂಕ್ತವಾದ ಗ್ರೈಂಡಿಂಗ್ ಡಿಸ್ಕ್ ಅನ್ನು ಆಯ್ಕೆ ಮಾಡುವುದು ಯಶಸ್ವಿ ಲೋಹದ ಕೆಲಸ ಮತ್ತು ತಯಾರಿಕೆಯ ಫಲಿತಾಂಶಗಳನ್ನು ಸಾಧಿಸುವಲ್ಲಿ ನಿರ್ಣಾಯಕ ಅಂಶವಾಗಿದೆ. ಆಯ್ಕೆಯು ಕೆಲಸ ಮಾಡುತ್ತಿರುವ ವಸ್ತು, ಅಪೇಕ್ಷಿತ ಮುಕ್ತಾಯ ಮತ್ತು ಬಳಕೆಯಲ್ಲಿರುವ ಗ್ರೈಂಡರ್ ಪ್ರಕಾರದಂತಹ ವಿವಿಧ ಅಂಶಗಳನ್ನು ಅವಲಂಬಿಸಿರುತ್ತದೆ. ವಸ್ತು ಹೊಂದಾಣಿಕೆ, ಅಪಘರ್ಷಕ ಪ್ರಕಾರ, ಗ್ರಿಟ್ ಗಾತ್ರ, ಚಕ್ರ ಪ್ರಕಾರ, ಅಪ್ಲಿಕೇಶನ್, ಗ್ರೈಂಡರ್ ಹೊಂದಾಣಿಕೆ, ಕಾರ್ಯ ನಿರ್ದಿಷ್ಟತೆ, ಸುರಕ್ಷತೆ, ಬ್ರ್ಯಾಂಡ್ ಗುಣಮಟ್ಟ ಮತ್ತು ವೆಚ್ಚವನ್ನು ಪರಿಗಣಿಸುವ ಮೂಲಕ, ನಿರ್ವಾಹಕರು ತಮ್ಮ ಗ್ರೈಂಡಿಂಗ್ ಪ್ರಕ್ರಿಯೆಗಳಲ್ಲಿ ದಕ್ಷತೆ ಮತ್ತು ಸುರಕ್ಷತೆಯನ್ನು ಹೆಚ್ಚಿಸಲು ತಿಳುವಳಿಕೆಯುಳ್ಳ ನಿರ್ಧಾರಗಳನ್ನು ತೆಗೆದುಕೊಳ್ಳಬಹುದು.
ಸುರಕ್ಷತಾ ಮಾರ್ಗಸೂಚಿಗಳನ್ನು ಪಾಲಿಸುವುದು, ಸೂಕ್ತವಾದ ವೈಯಕ್ತಿಕ ರಕ್ಷಣಾ ಸಾಧನಗಳನ್ನು ಧರಿಸುವುದು ಮತ್ತು ಗ್ರೈಂಡರ್ ಮತ್ತು ಡಿಸ್ಕ್ ಹೊಂದಾಣಿಕೆಗಾಗಿ ತಯಾರಕರ ಶಿಫಾರಸುಗಳನ್ನು ಅನುಸರಿಸುವುದು ಅತ್ಯಗತ್ಯ. ಭಾರೀ ಸ್ಟಾಕ್ ತೆಗೆಯುವಿಕೆ, ಮೇಲ್ಮೈ ಪೂರ್ಣಗೊಳಿಸುವಿಕೆ ಅಥವಾ ಕತ್ತರಿಸುವ ಅನ್ವಯಿಕೆಗಳಿಗಾಗಿ, ಸರಿಯಾದ ಗ್ರೈಂಡಿಂಗ್ ಡಿಸ್ಕ್ ಕೆಲಸದ ಗುಣಮಟ್ಟ ಮತ್ತು ದಕ್ಷತೆಯ ಮೇಲೆ ಗಮನಾರ್ಹವಾಗಿ ಪರಿಣಾಮ ಬೀರುತ್ತದೆ.
ಹೆಚ್ಚುವರಿಯಾಗಿ, ಸವೆತ ಮತ್ತು ಹರಿದುಹೋಗುವಿಕೆಗಾಗಿ ಆವರ್ತಕ ಪರಿಶೀಲನೆಗಳು, ಅಧಿಕ ಬಿಸಿಯಾಗುವುದು ಮತ್ತು ಕಂಪನದ ಕಾಳಜಿಗಳಂತಹ ಸಮಸ್ಯೆಗಳನ್ನು ಪರಿಹರಿಸುವುದು ಮತ್ತು ಲೋಡಿಂಗ್ ಸಮಸ್ಯೆಗಳನ್ನು ಅರ್ಥಮಾಡಿಕೊಳ್ಳುವುದು ಗ್ರೈಂಡಿಂಗ್ ಡಿಸ್ಕ್ನ ಜೀವಿತಾವಧಿಯನ್ನು ಹೆಚ್ಚಿಸಲು ಮತ್ತು ಸ್ಥಿರವಾದ ಕಾರ್ಯಕ್ಷಮತೆಯನ್ನು ಖಚಿತಪಡಿಸಿಕೊಳ್ಳಲು ಕೊಡುಗೆ ನೀಡುತ್ತದೆ.
ಸಂಕ್ಷಿಪ್ತವಾಗಿ ಹೇಳುವುದಾದರೆ, ಗ್ರೈಂಡಿಂಗ್ ಡಿಸ್ಕ್ಗಳನ್ನು ಆಯ್ಕೆ ಮಾಡುವುದು, ಬಳಸುವುದು ಮತ್ತು ನಿರ್ವಹಿಸುವುದಕ್ಕೆ ಉತ್ತಮ ಮಾಹಿತಿಯುಕ್ತ ಮತ್ತು ವ್ಯವಸ್ಥಿತ ವಿಧಾನವು ಅತ್ಯುತ್ತಮ ಫಲಿತಾಂಶಗಳನ್ನು ಸಾಧಿಸಲು, ಉತ್ಪಾದಕತೆಯನ್ನು ಹೆಚ್ಚಿಸಲು ಮತ್ತು ಸುರಕ್ಷಿತ ಕೆಲಸದ ವಾತಾವರಣವನ್ನು ಖಚಿತಪಡಿಸಿಕೊಳ್ಳಲು ಪ್ರಮುಖವಾಗಿದೆ.
ಪೋಸ್ಟ್ ಸಮಯ: ಜನವರಿ-12-2024